Fitting the same brakes on trucks and trailers is becoming
Page 42
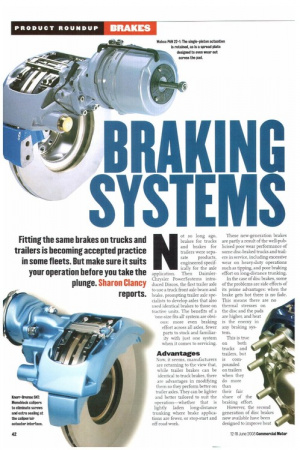
Page 43
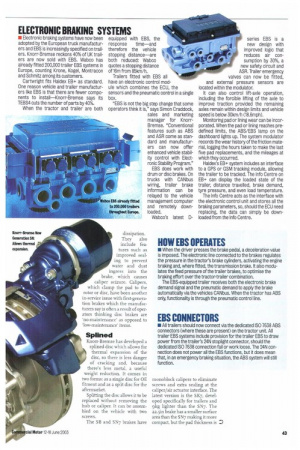
Page 44
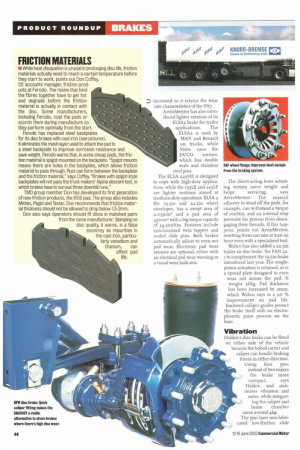
Page 45
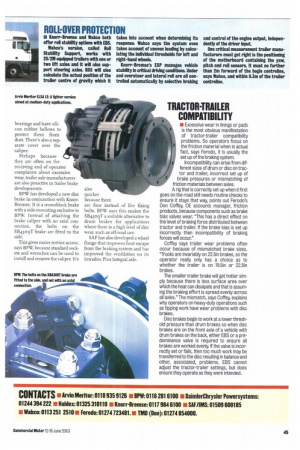
If you've noticed an error in this article please click here to report it so we can fix it.
accepted practice in some fleets. But make sure it suits your operation before you take the plunge. Sharon Clancy reports. Not so long ago, brakes for trucks and brakes for trailers were sepa
rate products, engineered specifically for the axle application. Then Daimler. Chrysler PowerSystems introduced Discos, the first trailer axle to use a truck front axle beam and brake, prompting trailer axle specialists to develop axles that also used identical brakes to those on tractive units. The benefits of a tone-size fits all' system are obvi ous: more even braking effort across all axles, fewer parts to stock arid familiar ity with just one system when it comes to servicing.
Advantages
Now, it seems, manufacturers are returning to the view that, while trailer brakes can be identical to truck brakes, there are advantages in modifying them so they perform better on
trailer axles. They can be lighter and better tailored to suit the operation—whether that is lightly laden long-distance trunking where brake applications are fewer, or stop-start and off-road work. These new-generation brakes are partly a result of the well-publicised poor wear performance of some disc-braked trucks and trailers in service, including excessive wear on heavy-duty operations such as tipping, and poor braking effort on long-distance trunking.
In the case of disc brakes, some of the problems are side effects of its prime advantages: when the brake gets hot there is no fade. This means there are no thermal stresses on the disc and the pads are higher, and heat is the enemy in any braking system.
This is true on both trucks and trailers, but is compounded on trailers when they do more than their fair share of the braking effort.
However, the second generation of disc brakes now available have been designed to improve heat dissipation.
They also include fea tures such as improved sealing to prevent water and dust ingress into the brake, which causes caliper seizure. Calipers, which clamp the pad to the rotor or disc, have been another in-service issue with first-generation brakes which the manufacturers say is often a result of operators thinking disc brakes are 'no-maintenance' as opposed to 'low-maintenance' items.
Splined
Knorr-Brenise has developed a splined disc which allows for thermal expansion of the disc, so there is less danger of cracking and, because there's less metal, a useful weight reduction. It comes in two forms: as a single disc for OE fitment and as a split disc for the aftermarket.
Splitting the disc allows it to be replaced without removing the hub or caliper. It can be assembled on the vehicle with two screws.
The SB and SN7 brakes have
monoblock calipers to eliminate screws and extra sealing at the caliper/air actuator interface. The latest version is the SK7, developed specifically for trailers and 9kg lighter than the SN7. The 22.5m brake has a smaller surface area than the SN7 making it more compact, but the pad thickness is D n increased so it retains the wear rate characteristics of the SN7. ArvinMeritor has also introduced lighter versions of its ELSA2 brake for trailer
applications. The ELSA2 is used by MAN and Renault on trucks, while Volvo uses the
D UCO version, which has double seals and stainless steel pins.
The ELSA 225HE is designed to cope with high-duty applications, while the i95LE and 225LE are lighter versions aimed at medium-duty operations. ELSA 2 fits 19.5in and 22.5in wheel envelopes, has a swept area of 2,o35cm2 and a pad area of 450cm2 with a big torque capacity of 34,5ooNm. Features include synchronised twin tappets and sealed slide pins. Both brakes automatically adjust to even out pad wear. Electronic pad wear sensors are optional, either with an electrical pad wear warning or a visual wear indicator.
The direct-acting lever actuating system saves weight and
helps servicing, says ArvinMeritor. The manual adjuster to wind off the pads, for example, can withstand a torque of iooNm, and an internal stop prevents the pistons from disengaging their threads. If this happens, points out ArvinMeritor, resetting them can take at least an hour even with a specialised tool.
Wabco has also added a 22.5in trailer air disc brake, the PAN 22i to complement the I 9.5fil brake introduced last year. The singlepiston actuation is retained, as is a spread plate designed to even
wear out across the pad. It weighs 36k5, Pad thickness has been increased by 2mm,
which Wabco says is a 20 % improvement on pad life. Enclosed calliper guides protect the brake itself with an electrophoretic paint process on the base.
Viwation
Haldex's disc brake can be fitted on either side of the vehicle because the bolted carrier and caliper can handle braking forces in either direction. Using four pins instead of two makes the brake more compact, says Haldex. and minimises vibration and noise, while integrating the caliper and brake chamber saves around 41c.g.
The pins have non-lubricated low-friction slide bearings and have silicon rubber bellows to protect them from dust. There's also a separate cover over the caliper.
Perhaps because they are often on the receiving end of operator complaints about excessive wear, trailer axle manufacturers are also proactive in trailer brake developments.
BPW has developed a new disc brake in conjunction with Knorr. Bremse. It is a monoblock brake with a side-mounting exclusive to BPW. Instead of attaching the brake caliper with an axial connection, the bolts on the SB43o9T brake are fitted to the side,
This gives easier service access, says BPW, because standard sockets and wrenches can be used to install and remove the caliper. It's
also quicker because there are four instead of five fixing bolts. BPW says this makes the SB43o9T a suitable alternative to drum brakes for applications where there is a high level of disc wear, such as off-road use.
SAF has also developed a wheel flange that improves heat escape from the braking system and has improved the ventilation on its Intradisc Plus Integral axle.