ROAD AND WORKSHOP by Handyman
Page 56
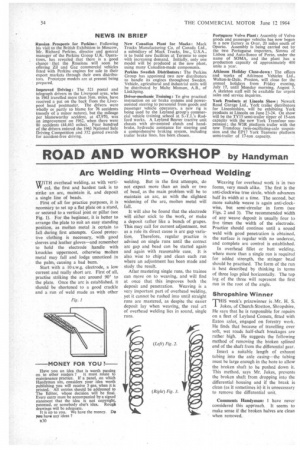
If you've noticed an error in this article please click here to report it so we can fix it.
Arc Welding Hints—Overhead Welding
WITH overhead welding, as with vertiVI' cal, the first and hardest task is to strike an arc, maintain it, and deposit a single line of beads. First of all for practice purposes, it is necessary to set up a flat plate on a stand, or secured to a vertical joist or pillar (see Fig. 1). For the beginner, it is better to arrange the plate to suit an easy standing position, as molten metal is certain to fall during first attempts. Good protective clothing is necessary, with good sleeves and leather gloves—and remember to hold the electrode handle with knuckles uppermost, otherwise molten metal may fall and lodge unnoticed in the palm, causing a bad burn. Start with a 10 s.w.g. electrode, a low current and really short arc. First of all, practise striking the arc around 90° to the plate. Once the arc is established, it should be shortened to a good crackle and a run of weld made as with other welding. But in the first attempts, do not expect more than an inch or two of bead, as the main problem will be to maintain an arc, as with the slightest widening of the arc, molten metal will fall.
it will also be found that the electrode will either stick to the work, or make a deposit rather like a bunch of grapes. This may call for current adjustment, out as a rule its direct cause is arc gap variation. Therefore, regular practice is advised on single runs until the correct arc gap and bead can be started again and again with reasonable ease. It is also wise to chip and clean each run where an adjustment has been made and study the result.
After mastering single runs, the trainee can move on to weaving, and will find at once that this improves both the deposit and penetration. Weaving is a very important part of overhead welding, yet it cannot be rushed into until straight runs are mastered, as despite the easier deposit lay when weaving, the real art of overhead welding lies in sound, single runs.
Weaving for overhead work is in two forms, very much alike. The first is the anti-clockwise true circle, which advances half its width at a time. The second, but more suitable weave is again anti-clockwise, but semi-circular in form (see Figs. 2 and 3). The recommended width of any weave deposit is usually four to five times the width of the electrode. Practice should continue until a sound weld with good penetration is obtained, the surface is regular with no undercut, and complete arc control is established.
In overhead fillet or butt welding, where more than a single run is required for added strength, the stringer bead should be practised. The form of the run is best described by thinking in terms of three logs piled horizontally. The top log of the three will represent the first run in the root of the angle.
Shropshire Winner 'THIS week's prizewinner, is Mr. H. S. I Jukes, of Church Stretton, Shropshire_ lie says that he is responsible for repairs on a fleet of Leyland Comets, fitted with Eaton axles, engaged on forestry work. He finds that because of travelling over soft, wet roads half-shaft breakages are rather high. He suggests the following method of removing the broken splined end of the shaft from the differential gear.
Insert a suitable length of exhaust tubing into the axle casing—the tubing must be large enough in the bore to allow the broken shaft to be pushed down it. This method, says Mr. Jukes, prevents the broken shaft from dropping into the differential housing and if the break is clean (as it sometimes is) it is unnecessary to remove the differential unit, Comments Handyman: 1 have never considered this approach. It seems to make sense if the' broken halves are clean when removed.