New battery's low
Page 47
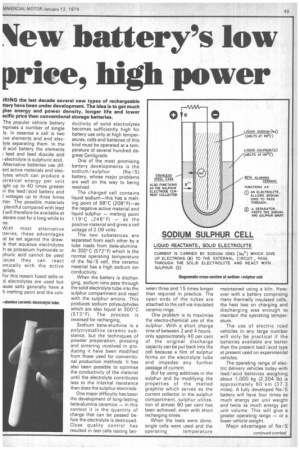
Page 48
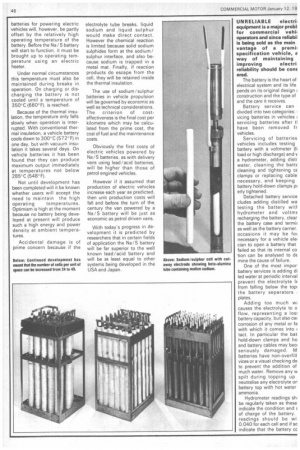
If you've noticed an error in this article please click here to report it so we can fix it.
price, high power
MING the last decade several new types of rechargeable ttery have been under development. The idea is to get much jher energy and power density, longer life and lower acific price than conventional storage batteries.
The popular vehicle battery -riprises a number of single Is. In essence a cell is two :ive elements and and eleclyte separating them. In the d acid battery the elements lead and lead dioxide and electrolyte is sulphuric acid. Alternative batteries use difent active materials and eleclytes which can produce a oretical energy per unit ight up to 40 times greater in the lead/acid battery and I voltages up to three times Iher. The possible materials plentiful compared with lead I will therefore be available at derate cost for a long while to ne.
With most alternative tteries, these advantages st be set against the draw:k that aqueous electrolytes :h as potassium hydroxide or phuric acid cannot be used :ause they can react .mically with the active terials.
For this reason fused salts or d electrolytes are used but :ause salts generally have a h melting point and the con ductivity of solid electrolytes becomes sufficiently high for battery use only at high temperatures, cells and batteries of this kind must be operated at a temperature of several hundred degrees Centigrade.
One of the most promising battery developments is the sodium/sulphur (Na/S) battery, whose major problems are well on the way to being resolved.
The charged cell contains liquid sodium—this has a melting point of 98cC (208'-'F)—as the negative active material and liquid sulphur — melting point 119"C i,246C F) — as the positive material and gives a cell voltage of 2.08 volts.
The two substances are separated from each other by a tube made from beta-alumina. At 300C (572'F) which is the normal operating temperature of the Na/S cell, this ceramic material has a high sodium ion conductivity.
When the battery is discharging, sodium ions pass through the solid electrolyte tube into the sulphur compartment and react with the sulphur anions. This produces sodium polysulphides which are also liquid at 300'C (572"F). The process is reversed for recharging.
Sodium beta-alumina is a polycrystalline ceramic substance, but the techniques of powder preparation, pressing and sintering involved in producing it have been modified from those used for conventional production methods. It has also been possible to optimise the conductivity of the material until the electrolyte contributes less to the internal resistance than does the sulphur electrode.
One major difficulty has been the development of long-lasting beta-alumina ceramics — in this context it is the quantity of charge that can be passed before the electrolyte is destroyed. Close quality control has resulted in test cells lasting bet ween three and 15 times longer than required in practice. The open ends of the tubes are attached to the cell via insulated ceramic rings.
One problem is to maximise the electro-chemical use of the sulphur. With a short charge time of between 2 and 4 hours, only approximately 40 per cent of the original discharge capacity can be put back into the cell because a film of sulphur forms on the electrolyte tube and impedes any further passage of current.
But by using additives in the sulphur and by modifying the properties of the matted graphite which serves as the current collector in the sulphur compartment, sulphur utilization of almost 90 per cent has been achieved, even with short recharging times.
When the tests were done, single cells were used and the operating temperature maintained using a kiln H owever with a battery comprising many thermally insulated cells, the heat loss on charging and discharging was enough to maintain the operating temperature.
. The use of electric road vehicles in any large number will only be practical if the batteries available are better than the present lead /acid type at present used on experimental vehicles.
The operating range of electric delivery vehicles today with lead/ acid batteries weighing about 1,000 kg (2,204 lb) is approximately 60 km (37.3 miles). A fully developed Na/S battery will have four times as much energy per unit weight and twice as much energy per unit volume. This will give a greater operating range — or a lower vehicle weight.
Major advantages of Na/S batteries for powering electric vehicles will, however, be partly offset by the relatively high operating temperature of the battery. Before the Na/S battery will start to function, it must be brought up to operating temperature using an electric heater.
Under normal circumstances this temperature must also be maintained during breaks in operation. On charging or discharging the battery is not cooled until a temperature of 350-:C (660'F). is reached.
Because of the thermal insulation, the temperature only falls slowly when operation is interrupted. With conventional thermal insulation, a vehicle battery cools down to 300C (572' F) in one day, but with vacuum insulation it takes several days. On vehicle batteries it has been found that they can produce maximum output immediately at temperatures not below 285C (548uF), Not until development has been completed will it be known whether users will accept the need to maintain the high operating temperatures. Optimism is high at the moment because no battery being developed at present will produce such a high energy and power density at ambient temperatures.
Accidental damage is of prime concern because if the electrolyte tube breaks, liquid sodium and liquid sulphur would make direct contact. However the chemical reaction is limited because solid sodium sulphides form at the sodium / sulphur interface, and also because sodium is trapped in a metal mat. Finally, if reaction products do escape from the cell, they will be retained inside the thermal insulation.
The use of sodium /sulphur batteries in vehicle propulsion will be governed by economic as well as technical considerations.
The criterion of costeffectiveness is the final cost per kilometre which may be calculated from the prime cost, the cost of fuel and the maintenance costs,
Obviously the first costs of electric vehicles powered by Na/S batteries, as with delivery vans using lead /acid batteries, will be higher than those of petrol engined vehicles.
However if it assumed that production of electric vehicles increase each year as predicted, then unit production costs will fall and before the turn of the century the van powered by a Na/S battery will be just as economic as petrol driven vans.
With today's progress in development it is predicted by researchers that in certain fields of application the Na/S battery will be far superior to the well known lead /acid battery and will be at least equal to other systems being developed in the USA and Japan.
UNRELIABLE electri, equipment is a major probl, for commercial vehil operators and since reliabil is being sold as the main vantage of a premii specification vehicle, a way of maintaining improving electri, reliability should be cons ered.
The battery is the heart of electrical system and its life pends on its original design construction and the type of and the care it receives.
Battery service can divided into two categories: : vicing batteries in vehicles ; servicing batteries after tl have been removed fr vehicles.
Servicing of batteries vehicles includes testing battery with a voltmeter (Ii load or high discharge) and v a hydrometer, adding disti water, cleaning the battE cleaning and tightening CE clamps or replacing cable necessary, and keeping battery hold-down clamps pi erly tightened.
Detached battery service eludes adding distilled wa testing the battery witf hydrometer and voltmE recharging the battery, clear the battery case and termit as well as the battery carrier. occasions it may be foi necessary for a vehicle elei cian to open a battery that failed so that its internal co lion can be analysed to de mine the cause of failure.
One of the most impor battery services is adding di led water at periodic interval prevent the electrolyte IE from falling below the top! the battery separators plates.
Adding too much causes the electrolyte to o flow, representing a los! battery capacity, but also cai corrosion of any metal or fa with which it comes into tact. In particular the bat hold-down clamps and ho and battery cables may beci seriously damaged. M batteries have non-overfill vices or a visual checking de to prevent the addition of much water. Remove any w spilt during topping up neutralise any electrolyte on battery top with hot water ammonia.
Hydrometer readings shi be regularly taken as these indicate the condition and E of charge of the battery. readings should be wi' 0,040 for each cell and if so indicate that the battery cc