The Vital Importance of Correct Lubrication
Page 48
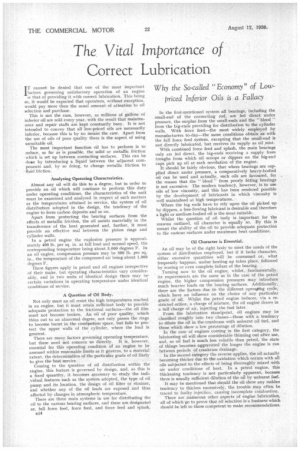
If you've noticed an error in this article please click here to report it so we can fix it.
Why the So-called "Economy" of Lowpriced Inferior Oils is a Fallacy
IT cannot be denied that one of the most important 'factors governing satisfactory operation of an engine is that of providing it with correct lubrication. This being so, it would be expected that operators, without exception, would pay more than the usual amount of attention to oil selection and purchase.
This is not the case, however, as millions of gallons of inferior oil are sold every year, with the result that maintenance and repair staffs are kept constantly busy. It is not intended to convey that all low-priced oils are necessarily inferior, because this is by no means the case. Apart from the use of oils of poor quality there is the aspect of using unsuitable oil.
The most important function oil has to perform is to reduce, so far as is possible, the solid or metallic friction which is set up between contacting surfaces. This can be done by introducing a liquid between the adjacent components and, by so doing, to change metallic friction to fluid friction.
Analysing Operating Characteristics.
Almost any oil will do this to a degree,. but in order to provide an oil which will continue to perform this duty under operating conditions, the characteristics of the unit must be examined and analysed in respect of such matters as the temperatures attained in service, the system of oil distribution adopted in the design, the tendency of the engine to form carbon deposits and so on.
Apart from protecting the bearing surfaces from the effects of metallic friction, the oil assists materially in the transference of the heat generated and, further, it must provide an effective seal between the piston rings and cylinder walls.
In a petrol engine the explosion pressure is approximately 400 lb. per sq. in, at full load and normal speed, the corresponding temperature being about 8,000 degrees F. In an oil engine, compression pressure may be 500 lb. per sq. in., the temperature of the compressed air being about 1,000 degrees F.
These figures apply in petrol and oil engines irrespective of their make, but operating characteristics vary considerably, and in two units of identical design there may becertain variations in operating temperature under identical conditions of service.
A Question of Oil Body.
Not only must an oil resist the high temperatures reached in an engine, but it must retain sufficient body to provide adequate protection to the frictional surfaces—the oil film must not become broken. An oil of poor quality, which thins out to an abnormal degree. not only passes the rings to become burnt in the comtsustion space, but fails to protect the upper walls of the cylinder, where the load is greatest.
There are many factors governing operating temperature, but these need not concern us directly. It is, however, essential for this operating condition of an engine to be assessed within reasonable limits as it governs, to a material extent, the determination of the particular grade of oil likely to give the best service Coming to the question of oil distribution within the engine, this feature is governed by design, and, as this is a fixed quantity, it becomes necessary to study the individual features such as the system adopted, the type of oil pump and its location„ the design of oil filter or strainer, and whether any of the oil leads are exposed and thus affected by changes in atmospheric temperature.
There are three main systems in use for distributing the oil to the various bearing surfaces, and these are.designated as, full force feed, force feed, and force feed and splash. 814 In the first-mentioned system all bearings, including the small-end of the connecting rod, are fed direct under pressure, the surplus from the small-ends and the " bleed " from the big-ends providing for distribution to the cylinder walls. With force feed—the most widely employed by manufacturers to-day—the same conditions obtain as with the full force feed system, excepting that the small-end is not directly lubricated, but receives its supply as oil tmist.
With combined force feed and splash, the main bearings only are fed direct. the big-ends receiving a supply from troughs from which oil scoops or dippers on the big-end caps pick up oil at each revolution of the engine.
It should be fairly obvious, that where bearings are supplied direct under pressure, a comparatively heavy-bodied oil can be used and actually, such oils are favoured, for the reason that the " bleed " from poorly fitting bearings is not excessive. The modern tendency, however, is to use oils of low viscosity, and this has been rendered possible by the development of lubricants in which viscosity is well maintained at high temperatures.
Where the big ends have to rely upon the oil picked up by dippers, a free-flowing lubricant is desirable and therefore a light or medium-bodied oil is the most suitable.
Whilst the question of oil body is important for the reasons outlined, oil character is equally so. By this is meant the ability of the oil to provide adequate protection to the various surfaces unaer maximum heat conditions.
Oil Character is Essential.
An oil may be of the right body to meet the needs of the system of distribution employed, but if it lacks character, either excessive quantities will be consumed or, what frequently happens, undue heating up takes place, followed by scoring or even complete failure of the bearing.
Turning now to the oil engine, whilst, fundamentally, its requirements are the same as in the case of the petrol engine, the higher compression pressures may introduce much heavier loads on the bearing surfaces. Additionally, there are the factors due to the different operating cycle, which have an influence on the choice of any particular grade of oil. Whilst the petrol engine induces, via a restricted orifice, a charge of mixture, the oil engine draws in a full charge of air, injecting the fuel later.
From the lubrication standpoint, oil engines may be classified roughly into two classes—those with a tendency to dilute the oil in the crankcase with unburnt oil fuel, and those which show a low percentage of dilution.
In the case of engines coming in the first category, the lubricating oil will show considerable thinning out after use, and, as oil fuel is much less volatile than petrol, the state of things becomes aggravated the longer the engine is run between periods of crankcase drainage.
In the second category the reverse applies, the oil actually becoming thicker due to the oxidation which occurs with all oils subjected to the effects of being thoroughly mixed with air under conditions of heat. In a petrol engine, this thickening tendency is not particularly apparent, because there is usually sufficient dilution of the oil by unburnt fuel.
It may be mentioned that should the oil show any sudden tendency to thicken excessively, the trouble may often be traced to faulty injection, causing incomplete combustion.
There are numerous other aspects of engine lubrication. all of which go to prove that oil selection is a business which should be left to those competent to make recommendations.