Some stark facts on missing spares
Page 72
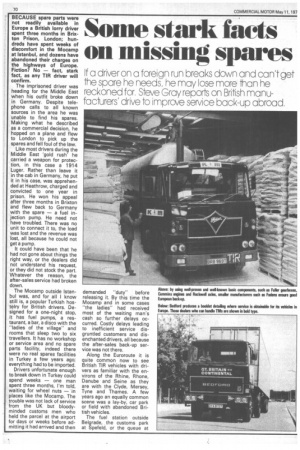
Page 73
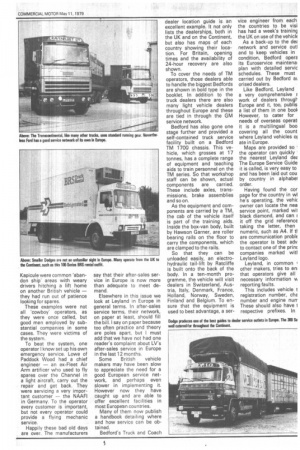
Page 74
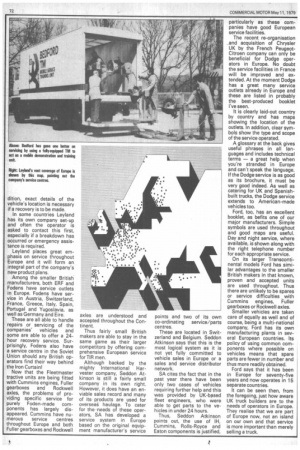
If you've noticed an error in this article please click here to report it so we can fix it.
If c driver on c foreign run crocks cown anc cc n't cet
--le score he neecs, he incy lose more an he
reckoned for. Steve Gray report on British manu
fac-urers' drive to inorove sevice occk-uo abrocd.
BECAUSE spare parts were not readily available in Europe a British lorry driver spent three months in Brixton Prison, London; hundreds have spent weeks of discomfort in the Mocamp at Istanbul, and dozens have abandoned their charges on the highways of Europe. Fiction? No — fact, stark fact, as any TIR driver will confirm.
The imprisoned driver was heading for the Middle East when his outfit broke down in Germany. Despite telephone calls to all known sources in the area he was unable to find his spares. Making what he described as a commercial decision, he hopped on a plane and flew to London to pick up the spares and fell foul of the law.
Like most drivers during the Middle East 'gold rush' he carried a weapon for protection, in this case a 1914 Luger. Rather than leave it in the cab in Germany, he put it in his case, was apprehended at Heathrow, charged and convicted to one year in prison. He won his appeal after three months in Brixton and flew back to Germany with the spare — a fuel injection pump. He need not have troubled. There was no unit to connect it to, the load was lost and the revenue was lost, all because he could not get a pump.
It could have been that he had not gone about things the right way, or the dealers did not understand his request, or they did not stock the part. Whatever the reason, the after-sales service had broken down.
The Mocamp outside Istanbul was, and for all I know still is, a popular Turkish hostelry for British drivers. Designed for a one-night stop, it has fuel pumps, a restaurant, a bar, a disco with the "ladies of the village" and rooms that sleep two to six travellers. It has no workshop or service area and no spare parts facility, indeed there were no real spares facilities in Turkey a few years ago; everything had to be imported.
Drivers unfortunate enough to break down in Turkey could spend weeks — one man spent three months, I'm told, waiting for wheel nuts in places like the Mocamp. The trouble was not lack of service from the UK but bloodyminded customs men who held the parcel at the airport for days or weeks before admitting it had arrived and then demanded "duty" before releasing it. By this time the Mocamp and in some cases "the ladies" had received most of the waiting man's cash so further delays occurred. Costly delays leading to inefficient service disgruntled customers and disenchanted drivers, all because the after-sales back-up service was not there.
Along the Euroroute it is quite common now to see British TIR vehicles with drivers as familiar with the environs of the Rhine, Rhone, Danube and Seine as they are with the Clyde, Mersey, Tyne and Thames. A few years ago an equally common scene was a lay-by, car park or field with abandoned British vehicles.
The fuel station outside Belgrade, the customs park at Spefeld, or the queue at Kapicule were common 'abandon ship' areas with weary drivers hitching a lift home on another British vehicle — they had run out of patience looking for spares.
These examples were not all 'cowboy' operators, as they were once called, but good men employed by substantial companies in some cases. They were victims of the system.
To beat the system, one operator I know set up his own emergency service. Lowe of Paddock Wood had a chief engineer — an ex-Fleet Air Arm artificer who used to fly spares over the Channel in a light aircraft, carry out the repair and get back, They were servicing a very important customer --the NAAFI in Germany. To the operator every customer is important, but not every operator could provide a flying mechanic service.
Happily these bad old days are over. The manufacturers say that their after-sales service in Europe is now more than adequate to meet demand, Elsewhere in this issue we look at Leyland in Europe in general terms. In after-sales service terms, their network, on paper at least, should fill the bill. I say on paper because too often practice and theory are poles apart, but I must add that we have not had one reader's complaint about LV's after-sales service in Europe in the last 12 months.
Some British vehicle makers may have been slow to appreciate the need for a good European service network, and perhaps even slower in implementing it. However now they have caught up and are able to offer excellent facilities in most European countries.
Many of them now publish a handbook detailing where and how service can be obtained.
Bedford's Truck and Coach dealer location guide is an excellent example. It not only lists the dealerships, both in the UK and on the Continent, but also has maps of each country showing their location. For Britain, opening times and the availability of 24-hour recovery are also shown.
To cover the needs of TM operators, those dealers able to handle the biggest Bedfords are shown in bold type in the booklet. In addition to the truck dealers there are also many light vehicle dealers throughout Europe and these are tied in through the GM service network.
Bedford has also gone one stage further and provided a self-contained truck service facility built on a Bedford TM 1700 chassis. This vehicle, which grosses at 17 tonnes, has a complete range of equipment and teaching aids to train personnel on the TM series. So that workshop staff can be shown, actual components are carried. These include axles, transmissions, brake assemblies and so on.
As the equipment and components are carried by a TM, the cab of the vehicle itself is part of the training aids. Inside the box-van body, built by Hawson Garner, are roller bearing rails on the floor to carry the components, which are clamped to the rails.
So that they can be unloaded easily, an electrohydraulic tail-lift by Ratcliffe is built onto the back of the body. In a ten-month programme, the vehicle will visit dealers in Switzerland, Austria, Italy, Denmark, France, Holland, Norway, Sweden, Finland and Belgium. To ensure that the equipment is used to best advantage, a ser
vice engineer from each the countries to be visi has had a week's training the UK on use of the vehicIE As a back-up to the dei network and service outl and to keep vehicles in condition, Bedford opera its Euroservice maintena plan with detailed servic schedules. These must carried out by Bedford at orised dealers.
Like Bedford, Leyland a very comprehensive r work of dealers through Europe and it, too, publis a list of them in one bool. However, to cater for needs of overseas operat it is a multilingual boo covering all the count where Leyland vehicles CI ate in Europe.
Maps are provided so the operator can quickly the nearest Leyland de The Europe Service Guide it is called, is very easy to and has been laid out cou by country in alphabei order.
Having found the cor page for the country in wl he's operating, the vehic owner can locate the nea service point, marked wii black diamond, and can I it off the grid reference taking the letter, then numeric, such as A4. If tl are communication problE the operator is best adv to contact one of the prim companies marked witl Leyland logo, Leyland, in common other makers, tries to en that operators give all necessary information reporting faults.
This includes vehicle t registration number, the
number and engine nunThese should also have 1 respective prefixes. In
dition, exact details of the vehicle's location is necessary if a recovery is to be made.
In some countries Leyland has its own company set-up and often the operator is asked to contact this first, especially if a breakdown has occurred or emergency assistance is required.
Leyland places great emphasis on service throughout Europe and it will form an integral part of the company's new product plans.
Among the smaller British manufacturers, both ERF and Fodens have service outlets in Europe. Fodens have service in Austria, Switzerland, France, Greece, Italy, Spain, Portugal and Yugoslavia, as well as Germany and Eire.
These are all able to handle repairs or servicing of the companies' vehicles and some are able to offer a 24hour recovery service. Surprisingly, Fodens also have a service centre in the Soviet Union should any British operators find their way behind the Iron Curtain!
Now that the Reetmaster tractive units are being fitted with Cummins engines, Fuller gearboxes and Rockwell axles, the problems of providing specific service for purely Foden-made components has largely disappeared. Cummins have numerous service centres throughout Europe and both Fuller gearboxes and Rockwell axles are understood and accepted throughout the Continent.
Thus fairly small British makers are able to stay in the same game as their larger competitors by offering comprehensive European service for TIR men.
Although backed by the mighty International Harvester company, Seddon Atkinson is still a fairly small company in its own right. However, it does have an enviable sales record and many of its products are used for overseas haulage. To cater for the needs of these operators, SA has developed a service system in Europe based on the original equipment manufacturer's service points and two of its own co-ordinating service/parts centres.
These are located in Switzerland and Belgium. Seddon Atkinson says that this is the most logical system as it is not yet fully committed to vehicle sales in Europe or a sales and service distributor network.
SA cites the fact that in the past year there have been only two cases of vehicles requiring further help and this was provided by UK-based fleet engineers, who were able to get parts to the vehicles in under 24 hours.
Thus, Seddon Atkinson points out, the use of IH, Cummins, Rolls-Royce and Eaton components is justified, particularly as these companies have good European service facilities.
The recent re-organisation and acquisition of Chrysler UK by the French PeugeotCitroen company can only be beneficial for Dodge operators in Europe. No doubt the service facilities in France will be improved and extended. At the moment Dodge has a great many service outlets already in Europe and these are listed in probably the best-produced booklet I've seen.
It is clearly laid-out country by country and has maps showing the location of the outlets. In addition, clear symbols show the type and scope of the service operated.
A glossary at the back gives useful phrases in all languages and includes technical terms — a great help when you're stranded in Europe and can't speak the language. If the Dodge service is as good as its brochure, it must be very good indeed. As well as catering for UK and Spanishbuilt trucks, the Dodge service extends to American-made vehicles too.
Ford, too, has an excellent booklet, as befits one of our major manufacturers. Simple symbols are used throughout and good maps are useful. Day and night service, where available, is shown along with the right telephone number for each appropriate service.
On its larger Transcontinental models Ford has similar advantages to the smaller British makers in that known, proven and accepted units are used throughout. Thus there are unlikely to be spares or service difficulties with Cummins engines, Fuller gearboxes or Rockwell axles.
Smaller vehicles are taken care of equally as well and of course, being a multi-national company, Ford has its own manufacturing plants in several European countries. Its policy of using common components where possible on vehicles means that spare parts are fewer in number and thus more readily obtained.
Ford says that it has been in Europe for seventy-five years and now operates in 15 separate countries.
It can be seen then, from the foregoing, just how aware UK truck builders are to the needs of operators in Europe. They realise that we are part of Europe now, not an island on our own and that service is more important than merely selling a truck.