POSSIBILITIES of WELDING ri CHASSIS CONSTRUCTION
Page 50

Page 51
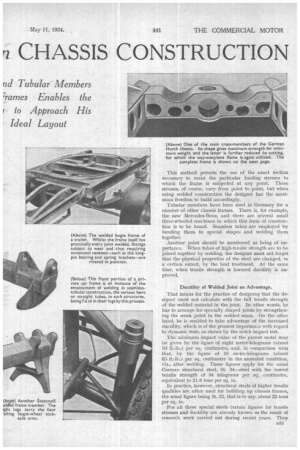
Page 52
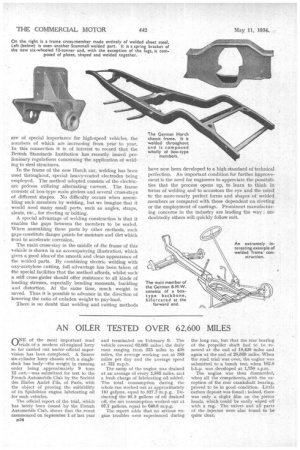
If you've noticed an error in this article please click here to report it so we can fix it.
The Use of Box-1y. in Welded Chassi: Designer More 117( Conception Of nd Tubular Members frames Enables the to Approach His Ideal Layout
BY the introduction of welding into chassis-frame construction, the use of new types of section has become possible. During the past two or three years a number of frame manufacturers has changed over from riveting to welding and the saving of a considerable amount of weight, especially when replacing steel castings by welded members, is thus accomplished.
The special advantages of box-type and tubular members are afforded not only by the saving in weight, but also by their neat and clean exteriors and by their high moments of inertia. The last-named represents better resistance to, and a lower deflection under, all classes of static and dynamic loads, buckling, bending and so forth. Danger of corrosion, furthermore, may be lower, frame repairs are simplified, and the need for riveting or bolting in assembly is avoided.
Certain shapes are manufactured by pressing or rolling flat steel plates (the former process produces a lighter part) and joining them by oxy-acetylene, electric-arc or resistance welding, and these three main methods have, to a large extent, been applied to chassis-frame building.
Prominent Concerns Already Adopting Welding.
Among British manufacturers which have largely adopted the welding process in building frame members are Scanunell Lorries, Ltd., John I. Thornycroft and Co., LW., and the Ford Motor Co., Ltd., whilst in Germany a number of prominent makers is employing similar methods. Cutting by the oxy-acetylene flame is indispensable when welding is to be applied to a large extent. Good combinations of cutting and welding in connection with tubular and box-type members are exemplified in the accompanying illustrations.
One of the pictures shows a form of tubular construction in which all the parts have been assembled intact by electric-arc welding. As may be seen, the finished structure gives a neat appearance without creating special danger points at which corrosion may arise.
In another illustration quite a new application of box construction is depicted. This specially shaped frame was built at the B.M.W. factory for a new vehicle which was shown for the first time at the Berlin Show held a few months ago. Such a form of main construction carried out in box section and forked, as shown in the drawing, would have been almost impracticable without the employment of welding.
B32 This method permits the use of the exact section necessary to resist the particular loading stresses to which the frame is subjected at any point. These stresses, of course, vary from point to point, but when using welded construction the designer has the maximum freedom to build accordingly.
Tubular members have been used in Germany for a number of other chassis frames. There is, for example, the new Mercedes-Benz, and there are several small three-wheeled machines in which this form of construction is to be found. Seamless tubes are employed by bending them to special shapes and welding them. together.
Another point should be mentioned as being of importance. When tubes of high-tensile strength are to be joined together by welding, the designer must not forget that the physical properties of the steel are changed, to a certain extent, by the heat treatment. At the same time, when tensile strength is lowered ductility is improved.
Ductility of Welded Joint art Advantage.
That means for the practice of designing that the designer must not calculate with the full tensile strength of the welded material in the joint. In other words, he has to arrange for specially shaped joints by strengthening the weak point in the welded seam. On the other hand, he is enabled to take advantage of the increased ductility, which is of the greatest importance with regard to dynamic tests, as shown by the notch impact test.
The minimum impact value of the parent metal may be given by the figure of eight metre-kilograms (about 50 ft.-lb.) per sq. centimetre, and, in comparison witrt that, by the figure of 10 metre-kilograms (about 6'5 ft.-lb.) per sq. centimetre in the annealed condition, viz., after welding. These figures apply for the usual German structural steel, St. 34—steel with the lowest tensile strength of 34 kilograms per sq. centimetre, equivalent to 21.6 tons per sq. in.
In practice, however, structural steels of higher tensile qualities are often used for building up chassis frames, the usual figure being St. 52, that is to say, about 33 tons per sq. in. •
• For all these special steels certain figures for tensile stresses and ductility are already known as the result of research work carried out during recent years. They n33 are of special importance for high-speed vehicles, the numbers of which are increasing from year to year. In this connection it is of interest to record that the British Standards Institution has recently issued preliminary regulations concerning the application of welding to steel structures.
In the frame of the new Horch car, welding has been used throughout, special heavy-coated electrodes being employed. The method adopted consists of the electricarc pr6cess utilizing alternating current. The frame consists of box-type main girders and several cross-stays of different shapes. No difficulty occurs when .assembling such members by welding, but we imagine that it would need many small parts, such as angles, straps, cleats, etc., for riveting or bolting.
A special advantage of welding construction is that it enables the gaps between the members to be sealed. When assembling these parts by other methods, such gaps constitute danger points for moisture and dirt which tend to accelerate corrosion.
The main cross-stay in the middle of the frame of this vehicle is shown in an accompanying illustration, which gives a good idea sof the smooth and clean appearance of the welded parts. By combining electric welding with oxy-acetylene cutting, full advantage has been taken of the special facilities that the method affords, whilst such a stiff cross-girder should offer resistance to all kinds of loading stresses, especially bending moments, buckling and distortion. At the same time, much weight is saved. Thus it is possible to advance in the direction of lowering the ratio of unladen weight to pay-load.
There is no doubt that welding and cutting methods have now been developed to a high standard of technical perfection. An important condition for further improvement is the need for engineers to appreciate the possibili ties that the process opens up, to learn to think in
terms of welding and to accustom the eye and the mind to the more-nearly perfect forms and shapes of welded. members as compared with those dependent on riveting or the employment of castings. Prominent manufactur ing concerns in the industry are leading the way ; undoubtedly others will quickly follow suit.