Interesting Tests on Composite Brake Drums
Page 45
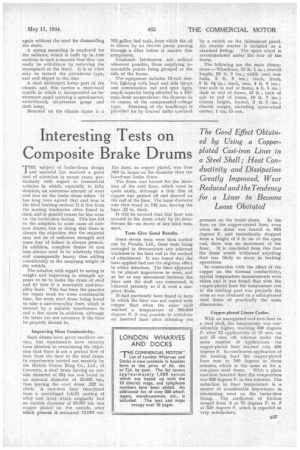
If you've noticed an error in this article please click here to report it so we can fix it.
The Good Effect Obtained by Using a Copper. plated Cast-iron Liner in a Steel Shell; Heat Conductivity and Dissipation Greatly Improved, Wear Reduced and the Tendency for a liner to Become Loose Obviated
THE subject of brake-drum design and material has received a great deal of attention in recent years, particularly with regard to commercial vehicles in which, especially in hilly districts, an enormous amount of wear and tear on the brake drum arises. It has long been agreed that cast iron is the ideal braking -surface. It is free from the scoring tendencies often found in steel, and in general causes far less wear on the brake-shoe facing. This has led to the adoption in some cases of castiron drums, but in doing this there is always the objection that the material may not be of sufficient strength and some fear of failure is always present. In addition, complete drums of cast iron always need to be relatively thick and consequently heavy, thus adding considerably to the unsprung weight of the vehicle.
The solution with regard to saving in weight and improving in strength appears to be to make the drum of steel and fut into it a renewable cast-ironalloy liner. This has been the practice for repair work for some considerable time, the worn steel drum being bored to take a cast-iron-alloy liner, which is secured by a suitable interference fit and a few rivets in addition; although the latter are not necessary if the liner be properly shrunk in., Improving Heat Conductivity.
Such drums have given excellent service, but experiments have recently been directed to overcoming the objection that there is not a perfect flow of heat from the liner to the steel drum. In experiments carried out recently by the British Piston Ring Co., Ltd., of Coventry, a. steel drum having an outside diameter of 151 ins. was bored to an internal diameter of 15.055 ins., thus leaving the steel drum .222 in. thick. A cast-iron liner (machined from a centrifugal (chill) casting of alloy cast iron) which originally had an outside diameter of 15.053 ins was copper plated on the outside, after which process it measured 15.079 ins. The liner, as copper plated, was thus -.024 in. larger on the diameter than the bored-out brake drum.
The drum was heated for the insertion of the cold liner, which went in quite easily, although a thin film of copper was pushed off and showed on the end of the liner. The inner diameter was then trued to 14i ins., leaving the liner .15 in. thick.
It will be noticed that this liner was secured in the drum solely hy its interference fit—no rivets of any kind were Tests Give Good Results.
Some severe tests were then carried out by Ferodo, Ltd., these tests being arranged to demonstrate any inherent weakness in the liner and in the method of attachment. It was found that the tests applied had not the slightest effect in either direction. The liner abpeared to be almost impervious to Wear, and so far as any movement between the liner and the shell was concerned, it behaved precisely as if it were a onepiece drum.
It had previously been found in tests in which the liner was not coated with copper that when the outer shell reached a temperature of 500-600 degrees F. it was possible to withdraw an inserted liner after releasing the pressure on the brake shoes. In the tests on the copper-coated liner, even when the drum was heated to 650 degrees F. and immediately dropped from a height of 3 ft. on to the open end, there was no movement of the liner. It is concluded from this that the drum wduld withstand anything that was likely to occur in braking operations.
In connection with the effect of the copper on the thermal conductivity, special temperature measurements were taken and it was found that with the copper-plated liner the temperature rise in the rubbing part was precisely the same as was obtained on a solid-pressed steel drum of practically the same dimensions.
Copper-plated Liners Cooler.
With an uncoppered cast-iron liner in a steel shell, the temperature was considerably higher, reaching 560 degrees F. after 12 applications of 15 secs. on and 15 secs. off, whereas under the same number of applications the copper-plated liner reached only 450 degrees F. In continuous application of the braking load the copper-plated liner rose to 540 degrees in three minutes, which is the same as for a one-piece steel drum. With a plain cast-iron inserted liner the temperature was 620 degrees F. in two minutes. The reduction in liner temperature is a matter of considerable importance in minimising wear on the brake-shoe lining. The coefficient of friction ranged from .4 at 70 degrees F. to .3 at 520 degrees P, which is regarded as very satisfactory.