HOW TO AVOID BROKEN PETROL PIPES.
Page 60
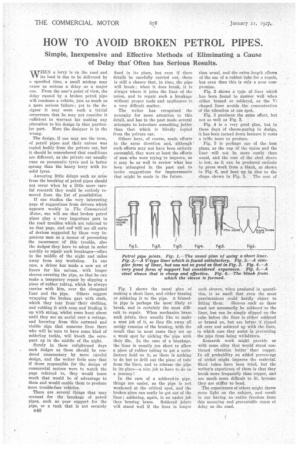
If you've noticed an error in this article please click here to report it so we can fix it.
Simple, Inexpensive and Effective Methods of Eliminating a Cause of Delay that' Often has, Serious Results.
IXTELEN a lorry is on the road and V V its load is due to be delivered by a specified time, a small mishap may cause as serious a delay as a major one. From the user's point of view, the delay caused by a broken petrol pipe will condemn a vehicle, just as much as a more serious failure; yet to the designer it may seem such a trivial occurrence that he may not consider it sufficient to warrant his making any alteration to his design in that particular part. Here the designer is in the wrong.
The design, if one may use the term, of petrol pipes and their unions was copied bodily from the private car, but it should be remembered that conditions are different, as the private car usually runs on pneumatic tyres and is better sprung than the heavy lorry with its solid tyres.
Annoying little delays such as arise from the breaking of petrol pipes should not occur when by a little more careful research they could be entirely removed from the list of possibilities.
If one studies the very interesting page of suggestions from drivers which appears weekly in The Commercial Motor, one will see that broken petrol pipes play a very important part in the road troubles which are referred to on that page, and on will see all sorts of devices suggested by these very ingenious men as a means of preventing the recurrence of this trouble, also the dodges they have to adopt in order quickly to repair such breakages—often in the middle of the night and miles away from any workshop. In one ease, a driver has made a new set of liners for • his unions, with longer sleeves covering the pipe, so that be can make a temporary repair by slipping a piece of rubber tubing, which he always carries with him, over the elongated
liner and the pipe. Others suggest wrapping the broken part with cloth, which they tear from their clothing, and rubbing it with soap and binding it up with string, whilst some hunt about until they see an atrial over a cottage, and knowing from this outward and visible sign that someone lives there who will be sure to have some kind of soldering tackle, will knock the occupant up in the middle of the night.
Surely in these enlightened days such dodges as these should be rendered unnecessary by more careful design, and the writer feels sure that if those responsible for the design of commercial motors were to watch the page referred to, they would learn much that would be of advantage to them and would enable them to produce more trouble-free vehicles.
There are several things that may account for the breakage of petrol pipes, such as poor support for the pipe, or a tank that is not securely B40
fixed in its place, but even if these details be carefully carried out, there is still a chance that, in time, the pipe will break ; when it does break, it is always where it joins the liner of the union, and to repair such a breakage without proper tools and appliances is a very difficult matter.
The writer has recognized the necessity for more attention to this detail, and has in the past made several attempts to introduce something better than that which is blindly copied from the private car.
Others have, of course, made efforts in the same direction and, although such efforts may not have been entirely successful, they were at least the efforts of men who were trying to improve, so it may be as well to review what has been attempted in the past and to invite suggestions for improvements that might be made in the future.
Fig. 1 shows the usual plan of making a short liner, and either brazing or soldering it to the pipe. A brazedin pipe is perhaps the most likely to break, and is certainly the most difticult to repair. When mechanics braze such joints, they usually like to make a neat job of it so they he away all untidy remains of the brazing, with the result that in most cases they set up a weak spot by nicking the' pipe with their file. In the case of a breakage, the liner is usually ,too short to allow a piece of rubber tubing to get a satisfactory hold on it, so there is nothing to do but to drill out the piece of tube from the liner, and to rebraze the pipe in its plaae—a nice job to have to do on a journey!
In the case of a soldered-in pipe, things are easier, as the pipe is not weakened at the critical spot, and the broken piece can easily be got out of the liner ; soldering, again, is an easier job than brazing brass. Soldered joints will stand well if the liner is longer than usual, and the extra length allows of the use of a rubber tube for a repair, but even then this is only a poor compromise.
Fig. 2 shows a typo of liner which has been found to answer well when either brazed or soldered, as the Yshaped liner avoids the concentration of the vibration at one spot.
Pig. 2 produces the same effect, but not so well as Pig. 2.
Fig. 4 is a very good plan, but in these days of cheese-paring in design, it has been turned down because it costs a trifle more to produce.
Fig. 5 is perhaps one Of the best plans, as the cap of the union and the liner will not be more costly than usual, and the cost of the steel sleeve is low, as it can he produced entirely by press work from a blank, as shown in Fig. 6, and bent up in dies to the shape shown in Fig. 5. The cost of
such sleeves, when produced in quantities, is so small that eventhe most parsimonious could hardly object to
fitting them. Sleeves such as these need not necessarily be soldered to the liner, but can be simply slipped on the tube before the liner is either soldered or brazed on, but are better, if tinned all over and soldered up with the liner, in which case they assist in preventing the pipe from being withdrawn. '
Research work might provide ue with some allay that would stand continued vibration better' than copper. In all probability an added percentage of nickel might improve the material. Steel tubes have been tried, but the writer's experience of them is that they break more frequently than copper, and are much more difficult to fit, because they are stiffer to bend.
The experiences of others might throw more light on the subject, and result in our having an entire freedom from this annoying and preventable cause of delay on the road.