The Metallurgist's Part in Vehicle Efficiency
Page 18
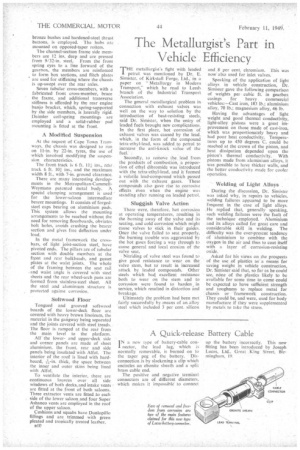
If you've noticed an error in this article please click here to report it so we can fix it.
THE metallurgist's fight with leaded petrol was mentioned by Dr. E. Simister. of Kirkstall Forge, Ltd., in a paper on "Metallurgy in Modern Transport," which he read to Leeds branch of the Industrial Transport Association.
The general metallurgical problem in connection with exhaust valves was well on the way to solution by the introduction of heat-resisting steels. said Dr. Simister, when the entry of leaded fuels brought new complications. In the first place, hot corrosion of exhaust valves was caused by the lead. which, in the form of the compound tetra-ethyl-lead, was added to petrol to increase the anti-knock value of the fuel.
Secondly, to remove the lead from the products of combustion, a proportion of ethyl dibromide was introduced with the tetra-ethyl-lead, and it formed a volatile lead-compound which passed out with the exhaust gases. These compounds also gave rise to .corrosive effects even when the engine was standing after running on leaded petrol.
Sluggish Valve Action There were, therefore, hot corrosion at operating temperatures, resulting in the burning away of the valve and its seating, and cold corrosion' which might cause valves to stick in their guides. Once the valve failed to seat properly, the burning trouble was aggravated by the hot gases forcing a way through to cause general and local erosion of the valve seat.
Nitriding of valve steel was found to give good resistance to wear on the valve stem, but to result in increased attack by leaded compounds. Other steels which had excellent resistance both to wear on the stem and to corrosion were found to harden . in service, which resulted in distortion and breakage.
Ultimately the problem had been met fairly successfully by means of an alloy steel which included 3 per cent. silicon
and ,8 per cent. chromium. This was now also used for inlet valves.
Speaking of the application of light alloys in vehicle construction, Dr. Sinister gave the following comparison of weights per cubic ft. in gearbox casings for heavy commercial vehicles:—Cast iron, 183 lb.; aluminium alloy, 70 lb.; magnesium alloy, 46 lb.
Having the advantages of light weight and good thermal conductivity, light-alloy pistons were a great improvement on those made of east-iron. which was proportionately heavy and had poor heat conductivity. Temperatures up to 450 degrees C. could be reached at the crown of the piston, and heat dissipation depended upon the piston's thermal conductivity. With pistons made from aluminium alloys, it was possible to have thicker walls, and the better conductivity made for cooler operatiOn.
Welding of Light Alloys
During the discussion, Dr. Simister was asked why, in repairs to vehicles. welding failures appeared to be more frequent in the case of light alloys. He replied that, generally speaking, such welding failures were the fault of the technique employed. Aluminium and its alloys called for great care and considerable skill in welding. The difficulty was the ever-present tendency of aluminium to combine with the oxygen in the air and thus to coat itself with a layer of corrosion-resisting oxide.
Asked for his views on the prospects of the use of plastics as a means for saving weight in vehicle construction, Dr. Simister said that, so far as he could see, none of the plastics likely to be available for some time to come could be expected to have sufficient strength and toughness to replace metal for chassis or 'framework construction. They could be, and were, used for body manufacture if they were supplemented by metals to take the stress.