Laboratory Support for Metallurgical Practice
Page 34
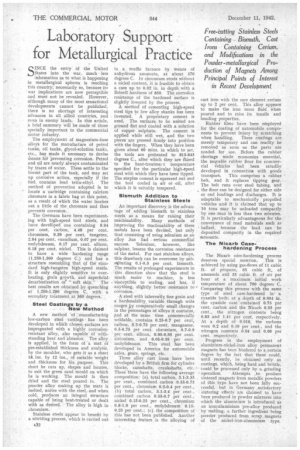
Page 35
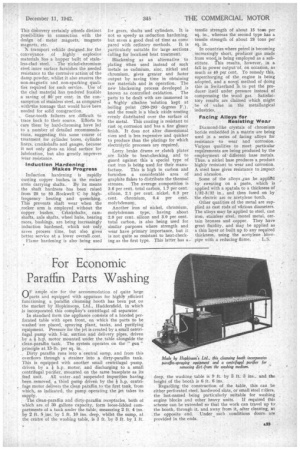
If you've noticed an error in this article please click here to report it so we can fix it.
C INCE the entry of the United OStates into the war, much less information as to what is happening in metallurgical spheres is reaching this country; necessarily so, because its war implications are now perceptible and must not be revealed. However, although many of the most sensational developments cannot be published, there is no shortage of interesting advances in all allied countries, and even in enemy lands. In this article, a brief summary will be made of those specially important to the commercial motor industry.
The employment of magnesium-base alloys for the manufacture of petrol tanks, oil tanks, glycol-solution tanks, etc., has made it necessary to devise Means for 'preventing corrosion. Petrol and oil are nearly always contaminated by traces of water. These settle to the lowest part of the tank, and may set up corrosive action, especially if the fuel contains lead tetra-ethyl. The method of prevention adopted is to locate a cartridge containing calcium chromate in a fabric bag at this point, as a result of which the water leaches out a little of the chromate and thus prevents corrosion.
The Germans have been experimenting with high-speed tool steels, and have develtped one containing 0.94 per cent. carbon. 4.48 per cent. chromium, 9.39 per cent. tungsten, 2.04 per cent. vanadium, 0.07 per cent.
molybdenum, 0.17 per cent. silicon, 0.18 per cent, nickel. This is claimed to have a wide • hardening range (1,250-1,300 degrees C.) and has a structure resembling that ef the stan
dard high-tungsten high-speed steels. It is only slightly sensitive to overheating, grain growth, and Superficial. decarburization of "soft skin.." The best results are obtained by quenching at 1,250-1,280 degrees C. with a secondary treatment at 560 degrees.
Steel Castings by a New Method A new method 'of manufacturing low-carbon steel castings has been developed in which chosen surfaces are impregnated with a highly corrosionresistant alloy, also capable of withstanding heat and abrasion. . The ahoy is applied; in the form of a mat of pre-established thickness and analysis, by the moulder, who gets it as a sheet 18, ins. by 12 ins„ of suitable weight and thickness for his purpose. This sheet he cuts up, shapes and locates, to suit the green sand mould on which be is working. The mould is then dried and the steel poured in. The powder alloy making up the mats is melted, unites with the steel, and when cold, produces an integral structure capable of being heat-treated or dealt with as desired. The alloy is high in chromium.
Stainless steels appear to benefit by a nitriding process, which is carried out
in a muffle furnace by means of anhydrous ammonia, at about 570 degrees C. in chromium steels without a nickel content, it is feasible to obtain a case up to 0,02 in, in depth with a Brinell hardness of 850. The corrosion resistance of the hardened surface is slightly lowered by the process. A method of cementing high-speed steel tips to low alloy shanks has been invented. A proprietary cement is used. The surfaces to be united are ground at and coated with a solution of copper sulphate. The cement is applied while still wet, and the two pieces are pressed firmly into position with the fingers. When they have been given about 66 mins, in which to set, the tools are preheated to 815-845 degrees C., after which they are faised to the heat-treatmert temperature specified for the particular high-speed steel with which they have been tipped. The surplus cement is squeezed out and the tool cooled in air or -oil, after which it is suitably tempered.
Bismuth Addition to
Stainless Steels
An important discovery is the advantage of adding bismuth to stainless steels as a means for raising their machinability. Many methods of improving the n-tachinability of these metals have been devised, but only that consisting of using selenium as an alloy ,has had • serious commertial success. 'Selenium, however, like sulphur, lessens the corrosion resistance of the metal. For cast stainless alloys, this drawback can be overcome by subssituting 0.1-0.5 per cent. bismuth. The results of prolonged experiments in 'this direction show that the steel is much easier to machine, is less 'susceptible to scaling, and has, if anything, slightly better resistance to corrosion.
A steel with inherently fine grain and a hardenability. variable through wide ranges ,py comparatively small changes in the percentages of alloys it contains, And at the same time commercially weldable, contains 0.25-0.7 per cent; carbon, 0.5-0.75 per cent, manganese, 0.5-0.75 per cent. chromium, 0.7-0.9 per cent. silicon, 0.05-0.35 per cent. zirconium, and 0.05-0.35 per cent. molybdenum. This steel has been developed in America for automobile axles, gears, springs, etc.
Three alloy cast irons have been developed by a British firm for cylinder blocks, camshafts, crankshafts, etc.
These three have the following average composition: (a) total carbon, 3.1-3.35
per cent., combined carbon 0.55-0.75 per cent., chromium 0.2-0.4 per cent., (b) total carbon, 3.1-3.4 per cent.,
combined carbon 0.55-0.7 per cent., nickel 0.15-0.25 per cent., chromium 0.8-1.0 per cent., molybdenum 0.150.25 per cent.: (c) . the composition of this has not been published. Another interesting feature is the alloying of
cast iron with the rare element cerium up to 2 per cent. This alloy appears to make the iron more fluid when poured and to raise its tensile and bending properties.
Rubber films have been employed for the Coating of automobile components to prevent injury by scratching
when handling. These coatings are merely temporary and can readily be remoired as soon as the parts are needed for use. Before the rubber shortage made economies essential, the unlivable rubber floor for commercial vehicles had been steadily developed in connection with goods
transport. This comprises a rubber belt, and it replaces tipping gear. The belt runs over steel tubing, and the floor can be designed for either side or end loadings and discharges. It is adaptable to mechanically propelled vehicles and it is claimed that 'up to 10 tons may be unloaded compactly by one man in less than two minutes. It is particularly advantageous for the conveyance of road materials such as ballast, because the load can be deposited compactly in the required amounts.
The Nicarb Case
hardening Process The Nicarb case-hardening process deserves special mention. This is achieved by using gas-flows of 11 cubic ft. of propane, 65 cubic ft_ of ammonia and 35 cubic ft. of air per hour at a maximum initial work temperature of about 700 degrees C. Comparing this process with the same type of steel case-hardened in a cyanide bath: at a. depth of 0.004 in. the cyanide case contained 0.75 per 'cent, carbon and the Nicarb 0.53 per cent., the nitrogen contents being 0.83 and 1.41 per cent. respectively. At a depth of 0.016, the carbons were 0.2 and 0.19 per cent., and the nitrogen contents 0.04 and 0.06 per cent. respectively.
Progress in the employment of aluminium-nickel-iron alloy permanent magnets has been hindered to a certain degree by the fact that these could, until recently, be obtained only as castings, which, being hard and brittle, • could be processed only by a grinding operation. Attempts ,to produce sintered magnets from metallic powders of this type have not been fully successful, but in Germany satisfactory sietering effects are claimed to have been produced in powder mixtures into which the 'aluminium is introduced is an iron-aluminium pre-alloy produced by melting, a further ingredient 'being powder produced from scrap magnets of the nickel-iron-aluminium type.
This discovery certainly affords distinct possibilities in connection with the design of meter magnets, magneto magnets, etc.
'A transport vehicle designed,for the conveyance of highly explosive materials has a hopper built of stain
less-clad steel. The nickel-chromium steel inner surface furnishes the needed resistance to the corrosive action of the damp powder, whilst it also ensures the non-magnetic and non-sparking qualities required for such service. Use of the clad material has rendered feasible a saving of so per cent, in the consumption of stainless steel, as compared witbithe tonnage -that would have been needed for solid construction.
Gear-tooth failures are difficult to trace back to their source. Efforts to cure them by hard-chroming have led to a number of detailed recommendations. suggesting this same course of treatment for cylinder, bores, cylinder liners, crankshafts and gauges, because it not only gives an ideal surface for lubrication, but also greatly improves wear resistance.
Induction Hardening Makes Progress Induction hardening is rapidly ousting copper bushes, in the rocker arms carrying shafts. By its means the shaft hardness has been raised from 20 to 50 Rockwell C by high. Frequency heating and quenching. This prevents shaft wear when the _rocker arm is employed without the copper bushes. Crankshafts, camshafts, axle shafts, wheel hubs, bearing races, bushings, are being increasingly induction hardened, which not only saves process time, but also gives better service at a lower overall cost.
Flame hardening is also being used for gears, shafts and cylinders. It is not so speedy as induction hardening, but saves a good deal of time as com pared with ordinary methods. It is particularly suitable for large sections . calling for localized heat treatment.
Blackening as an alternative to plating when used instead of such metals as cadmium, zinc, nickel and chromium,. gives greater and faster output by saving time in obtaining raw materials and in operation. The new blackening process developed is known as controlled oxidation. The parts to be dealt with are immersed in a highly alkaline 'solution kept at boiling point (290-295 degrees F.), and the result is a black okide coating evenly distributed over the surface of the metal. This coating is resistant to rust or corrosion and has a fine glossy finish. It does not alter dimensional sizes and is less expensive and quicker to produce than the platings for which electrolytic processes are required.
Lorry brake drums or clutch plates' are liable to heat-checking, and to guard against this a special type of cast iron is being used for their manufacture. This is high in carbon and furnishes a considerable area of graphite flakes to distribute the thermal
stresses. The average composition is 3.8 per cent, total carbon 1,7 per cent. silicon, 2.1 per cent. nickel, 0.3 per cent. chromium, 0.4 per cent. molybdenum:.
Another iron of nickel, chromium, molybdenum type, having about 2.0 per cent. silicon and 3:0 per cent. total carbon, is also being used for similar purposes where strength and wear have primary importance, but it is not quite so resistant to heat-checking as the first type. This latter has a—
tensile strength of about 15 tore per sq. in., whereas the second type has a tensile strength of about 28 tons per sq. in.
In countries where petrol is becoming increasingly short, producer gas made from wood6is being employed as a substitute. This results, however, in a fall in power output of, on occasion, as much as 40 per cent. To remedy this, supercharging of the engine is being adopted, and a novel method of doing this in Switzerland Is to put the produceritself under pressure instead of compressing the wood gas. Satisfactory results are claimed which might be of value in the metallurgical industries.
Facing Alloys for Resisting Wear Diamond-like crystals of chromium boride embedded in a matrix are being used in a series of facing alloys for resistance to wear and corrosion.
Various qualities to meet particular a requirements are being produced by the employment of different base metals. Thus, a nickel base produces a product highly resistant to wear and corrosion. A steel base gives resistance to impact and abrasion.
Some of the alloys „can be appliM by sweating on a paste. which i3 applied with a spatula to a thickness of. 1/32-3/32 in., and then fused on by the electric arc or acetylene torch.
Other qualities of the metal are supplied as cast rods of Various diameters. The alloys may be applied to steel, cast iron, stainless steel, monel metal, certain bronzes and copper. They have great fluidity, and may be applied as a thin layer or built up to any required thickness, using the acetylene blow
pipe with a reducing-flame. L.S: