:H1 branches out NOFRAME (Engineering) part of the Chris Hudson
Page 23
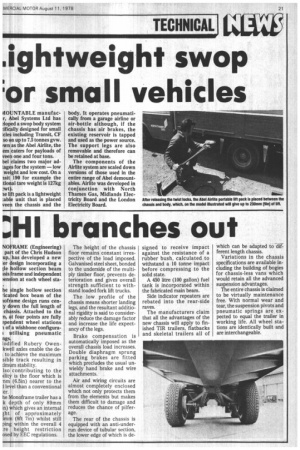
If you've noticed an error in this article please click here to report it so we can fix it.
up, has developed a new ler design incorporating a ;le hollow section beam tsis frame and independent wnsion at each wheel sta he single hollow section icated box beam of the toframe design runs ceny down the full length of chassis. Attached to the n, at four points are fully i!pendent wheel stations t of a wishbone configura utilising pneumatic ngs, Iodified Rubery Owenkwell axles enable the deto achieve the maximum sible track resulting in zimum stability.
lso contributing to the ility is the floor which is Tun (6.5in) nearer to the 1 level than a conventional ler.
he Monoframe trailer has a k depth of only 89mm in) which gives an internal ght of approximately imm (8ft 7in) whilst still ping within the overall 4 .re height restriction osed by EEC regulations. The height of the chassis floor remains constant irrespective of the load imposed. Galvanised steel sheet, bonded to the underside of the multiply timber floor, prevents deterioration and gives overall strength sufficient to withstand loaded fork lift trucks.
The low profile of the chassis means shorter landing legs, and the resultant additional rigidity is said to considerably reduce the damage factor and increase the life expectancy of the legs.
Brake compensation is automatically imposed as the overall chassis load increases. Double diaphragm sprung parking brakes are fitted which precludes the usual unwieldy hand brake and wire attachments.
Air and wiring circuits are almost completely enclosed which not only protects them from the elements but makes them difficult to damage and reduces the chance of pilferage.
The rear of the chassis is equipped with an anti-underrun device of tubular section, the lower edge of which is de signed to receive impact against the resistance of a rubber bush, calculated to withstand a 10 tonne impact before compressing to the solid state.
A 450 litre (100 gallon) fuel tank is incorporated within the fabricated main beam.
Side indicator repeaters are rebated into the rear-side raves.
The manufacturers claim that all the advantages of the new chassis will apply to finished TIR trailers, flatbacks and skeletal trailers all of which can be adapted to different length chassis.
Variations in the chassis specifications are available including the building of bogies for chassis-less vans which would retain all the advanced suspension advantages.
The entire chassis is claimed to be virtually maintenance free. With normal wear and tear, the suspension pivots and pneumatic springs are expected to equal the trailer in working life. All wheel stations are identically built and are interchangeable.