Prevention is Better than Cure
Page 41
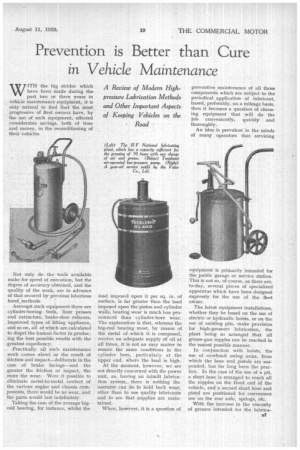
Page 42
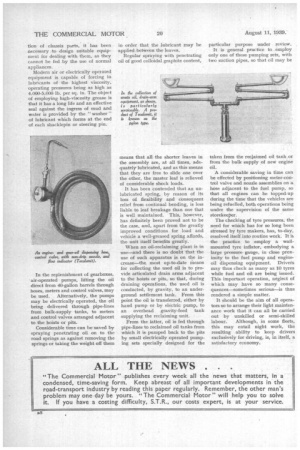
If you've noticed an error in this article please click here to report it so we can fix it.
in Vehicle Maintenance
A Review of Modern Highpressure Lubrication Methods and Other Important Aspects of Keeping Vehicles on the Road
WITH the big strides which have been made during the past two or three years in vehicle maintenance equipment, it is only natural to End that the most progressive of fleet owners have, by the use of such equipment, effected considerable savings, both of time and money, in the reconditioning of their vehicles.
Not only do the tools available make for speed of execution, but the degree of accuracy obtained, and the quality of the work, are in advance of that secured by previous laborious hand methods.
Amongst such equipment there are cylinder-boring tools, liner presses and extractors, brake-shoe refa,cers, improved types of lifting appliance, and so on, all of which are calculated to dispel the human factor in producing the best possible results with the greatest expediency.
Practically all such maintenance work comes about as the result of friction and impact—deliberate in the case of brake facings—and the greater the friction or impact, the more the wear. Were it possible to eliminate metal-to-metal contact of the various engine and chassis components, there would be no wear, and the parts would last indefinitely.
Taking the case of the average bigend bearing, for instance, whilst the load imposed upon it per sq. in. of surface, is far greater than the load imposed upon the piston and cylinder walls, bearing wear is much less pronounced than cylinder-bore wear. The explanation is that, whereas the big-end bearing must, by reason of the metal of which it is composed, receive an adequate supply of oil at all times, it is not an easy matter to ensure the same conditions in the cylinder bore, particularly at the upper end, Where the load is high.
At the moment, however, we are not directly concerned with the power unit, as, having an inbuilt lubrication system, there is nothing the operator can do to hold back wear, other than to use quality lubricants and to see that supplies are maintained.
When, however, it is a question of preventive maintenance of all those components which are subject to the periodical application of lubricant, based, preferably, on a mileage basis, then it becomes a question of choosing equipment that will do the job conveniently, quickly and thoroughly.
An idea is prevalent in the minds of many operators that servicing equipment is primarily intended for the public garage or service station. This is not so, of course, as there are, to-day, several pieces of specialized apparatus which have been designed expressly for the use of the fleet owner.
The latest equipment installations, whether they be based on the use of electric or hydraulic hoists, or on the use of existing pits, make provision for high-pressure lubrication, the plant being so arranged that all grease-gun nipples can be reached in the easiest possible manner.
In conjunction with hoists, the use of overhead swing arms, from which the hose and pistols are sus: pended, has for long been the practice. In the case of the use of a pit, a short hose is arranged to reach all the nipples on the front end Of the vehicle, and a second short hose and pistol are positioned for convenient use on. the rear axle, springs, etc.
With the increase in the viscosity of greases intended for the lubrica tion of chassis parts, it has been necessary to design suitable equipment for dealing with them, as they cannot be fed by the use of normal appliances.
Modern air or electrically operated equipment is capable of forcing in lubricants of the highest viscosity, operating pressures being as high as 4,000-5.000 lb. per sq. in. The object of employing high-viscosity grease is that it has a long life and an effective seal against the ingress of mud and water is provided by the " washer" of lubricant which forms at the end of each shacklepin or steering pin.
In the replenishment of gearboxes, air-operated pumps, lifting the oil direct from 40-gallon barrels through hoses, meters and control valves, may be used. Alternatively, the pumps may be electrically operated, the oil being delivered through pipe-lines from bulk-supply tanks, to meters and control valves arranged adjacent to the hoists or pits.
Considerable time can be saved by spraying penetrating oil on to the road springs as against removing the springs or taking the weight off them in order that the lubricant may be applied between the leaves.
Regular spraying with penetrating oil of good colloidal graphite content, means that all the shorter leaves in the assembly are, at all times, adequately lubricated, and as this means that they are free to slide one over the other, the master leaf is relieved of considerable shock loads.
It has been contended that an unlubricated spring, by reason of its loss of flexibility and consequent relief from continual bending, is less liable to leaf breakage than one that is well maintained. This, however, has definitely been proved not to be the case, and, apart from the greatly improved conditions for load and vehicle a well-greased spring affords, the unit itself benefits greatly.
When an oil-reclaiming plant is in use—and there is no doubt that the use of such apparatus is on the increase—the most up-to-date means for collecting the used oil is to provide articulated drain arms adjacent to the hoists or pits, so that, during draining operations, the used oil is conducted, by gravity, to an underground settlement tank. From this point the oil is transferred, either by hand pump or by electric pump, to an overhead gravity-feed. tank supplying the reclaiming unit.
From the latter, oil is fed through pipe-lines to reclaimed oil tanks from which it is pumped back to the pits by small electrically operated pumping sets specially designed for the particular purpose under review. It is general practice to employ only one of these pumping sets, with two suction pipes, so that oil may be taken from the reclaimed oil tank or from the bulk supply of new engine oil.
A considerable saving in time can be effected by positioning meter-control valve and nozzle assemblies on a hose adjacent to the fuel pump, so that all engines can be topped-up during the time that the vehicles are being refuelled, both operations being under the supervision of the same storekeeper.
The checking of tyre pressures, the need for which has for so long been stressed by tyre makers, has, to-day, resolved itself into routine work. It is the practice to employ a wallmounted tyre inflator, embodying a large pressure gauge, in close proximity to the fuel pump and engineoil dispensing equipment. Drivers may thus check as many as 10 tyres while fuel and oil are being issued. This important operation, neglect of which may have so many consequences—sometimes serious—is thus rendered a simple matter.
It should be the aim of all operators so to arrange their light maintenance work that it can all be carried out by unskilled or semi-skilled labour. Although, in some fleets, this may entail night work, the resulting ability to keep drivers exclusively for driving, is, in itself, a satisfactory economy.