CUTTING THE CRANE BILL
Page 53
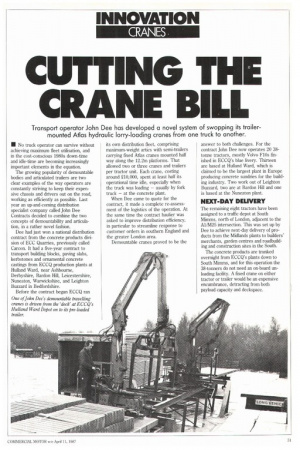
If you've noticed an error in this article please click here to report it so we can fix it.
• No truck operator can survive without achieving maximum fleet utilisation, and in the cost-conscious 1980s down-time and idle-time are becoming increasingly important elements in the equation.
The growing popularity of demountable bodies and articulated trailers are two clear examples of the way operators are constantly striving to keep their expensive chassis and drivers out on the road, working as efficiently as possible. Last year an up-and-coming distribution specialist company called John Dee Contracts decided to combine the two concepts of demountability and articulation, in a rather novel fashion.
Dee had just won a national distribution contract from the concrete products division of ECC Quarries, previously called Carcon. It had a five-year contract to transport building blocks, paving slabs, kerbstones and ornamental concrete castings from ECCQ production plants at HuIland Ward, near Ashbourne, Derbyshire, Bardon Hill, Leicestershire, Nuneaton, Warwickshire, and Leighton Buzzard in Bedfordshire.
Before the contract began ECCQ ran One of John Dee's demountable travelling cranes is driven from the 'dock' at ECCQ's Hunan-ft Ward Depot on to its pre-loaded trailer. its own distribution fleet, comprising maximum-weight artics with semi-trailers carrying fixed Atlas cranes mounted half way along the 112m platforms. That allowed two or three cranes and trailers per tractor unit. Each crane, costing around £10,000, spent at least half its operational time idle, especially when the truck was loading — usually by fork truck — at the concrete plant.
When Dee came to quote for the contract, it made a complete re-assessment of the logistics of the operation. At the same time the contract haulier was asked to improve distribution efficiency, in particular to streamline response to customer orders in southern England and the greater London area.
Demountable cranes proved to be the answer to both challenges. For the contract John Dee now operates 20 38tonne tractors, mostly Volvo FlOs finished in ECCQ's blue livery. Thirteen are based at Hulland Ward, which is claimed to be the largest plant in Europe producing concrete sundries for the building industry. Two work out of Leighton Buzzard, two are at Bardon Hill and one is based at the Nuneaton plant.
NEXT-DAY DELIVERY
The remaining eight tractors have been assigned to a traffic depot at South Mirnms, north of London, adjacent to the A1/M25 intersection. This was set up by Dee to achieve next-day delivery of products from the Midlands plants to builders' merchants, garden centres and roadbuilding and construction sites in the South.
The concrete products are trunked overnight from ECCQ's plants down to South Mimms, and for this operation the 38-tonners do not need an on-board unloading facility. A fixed crane on either tractor or trailer would be an expensive encumbrance, detracting from both payload capacity and deckspace.