How UK tippers cope in Scotland
Page 155
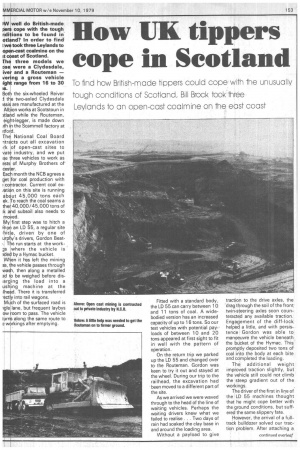
Page 156
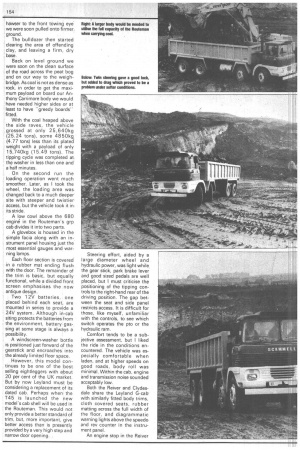
Page 157

Page 158
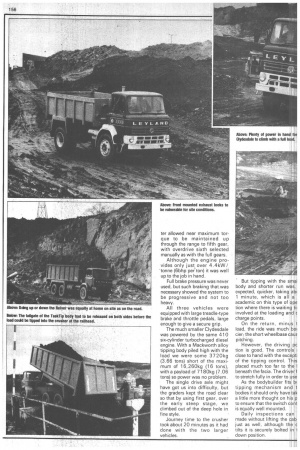
Page 159
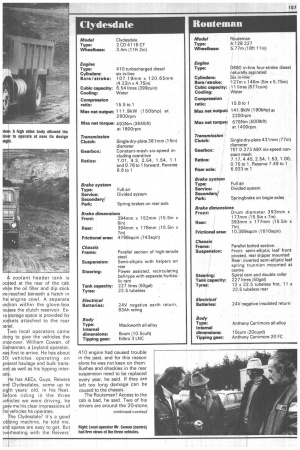
Page 160
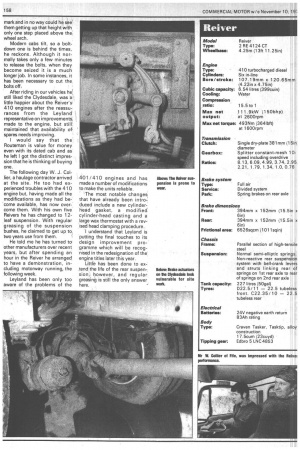
If you've noticed an error in this article please click here to report it so we can fix it.
To find how British-mace tippers could cope with the unusually tough conditions of Scotland, Bill Brock took nree Leylands to an open-cast coalmine on the east coast
well do British-made cope with the tough idi ions to be found in' otl nd? In order to find t we took three Leylands to open-cast coalmine on the it coast of Scotland.
three models we were a Clydesdale, and a Routeman — ng a gross vehicle range from 16 to 30
the OS
the six-wheeled Reiver e two-axled Clydesdale are manufactured at the ion works at Seotstoun in d while the Routeman, t-legger, is made down the Scam mell factory at d, National Coal Board cts out all excavation of open-cast sites to industry, and we put hree vehicles to work as of Murphy Brothers of cester.
Each month the NCB agrees a get for coal production with co tractor. Current coal extati n on this site is running ab ut 45,000 tons each ek. fT1 o reach the coal seams a ther 40,000/45,000 tons of lc ad subsoil also needs to Fro ed.
My first step was to hitch a Ieoi an LD 55, a regular site i e, driven by one of
L
Al
eig ith rtfo The itr rk vat ei
BSI
rphy's drivers, Gordon Beat,. The run starts at the works where the vehicle is aded by a Hymac bucket. When it has left the mining az, the vehicle passes through wash, then along a metalled ad to be weighed before dislarging the load into a us ing machine at the Ihe d. There it is transferred -ect y into rail wagons.
ML4ch of the surfaced road is lgle lane, but frequent laybys ow oom to pass. The vehicle turrs along the same route to a workings after emptying.
Fitted with a standard body, the LD 55 can carry between 10 and 11 tons of coal. A widebodied version has an increased capacity of up to 16 tons. So our test vehicles with potential pay-' loads of between 10 and 20 tons appeared at first sight to fit in well with the pattern of operation.
On the return trip we parked up the LD 55 and changed over to the Routeman. Gordon was keen to try it out and stayed at the wheel. During our trip to the railhead, the excavation had been moved to a different part of the site.
As we arrived we were waved through to the head of the line of waiting vehicles. Perhaps the waiting drivers knew what we failed to realise . . Two days of rain had soaked the clay base in and around the loading area.
Without a payload to give traction to the drive axles, the 'drag through the soil of the front twin-steering axles soon counteracted any available traction. Engagement of the diff-lock helped a little, and with persistence Gordon was able to manoeuvre the vehicle beneath the bucket of the Hymac. This promptly deposited two tons of coal into the body at each bite and completed the loading.
The additional weight improved traction slightly, but the vehicle still could not climb the steep gradient out of the workings.
The driver of the first in line of the • LD 55 machines thought that he might cope better with the ground conditions, but suffered the same slippery fate.
However, the arrival of a fulltrack bulldozer solved our traction problem. After attaching a
hawser to the front towing eye we were soon pulled onto firmer; ground.
The bulldozer then started clearing the area of offending clay, and leaving a firm, dry base.
Back on level ground we were soon on the clean surface of the road across the peat bog and on our way to the weighbridge. As coal is not as dense as rock, in order to get the maximum payload on board our Anthony Carrimore body we would have needed higher sides or at least to have "greedy boards'' fitted.
. With the coal heaped above the side raves, the vehicle grossed at only 25,640kg (25.24 tons), some 4850kg... (4.77 tons) less than its plated weight with a payload of only 15,740kg (15.49 tons). The tipping cycle was completed at the washer in less than one and a half minutes.
On the second run the loading operation went much smoother. Later, as I took the wheel, the loading area was changed back to a much deeper site with steeper and twistier access, but the vehicle took it in. its stride.
A low cowl above the 680 engine in the Routeman's grp cab divides it into two parts.
A glovebox is housed in the simple facia along with an instrument panel housing just the most essential gauges and warning lamps.
Each floor section is covered in a rubber mat ending flush: with the door. The remainder of the trim is basic, but equally functional, while a divided front screen emphasises the now antique design.
Two 12V batteries, one placed behind each seat, are mounted in series to provide a 24V system. Although in-cab siting protects the batteries from the environment, battery gassing at some stage is always a possibility.
A windscreen-washer bottle is positioned just forward of the gearstick and encroaches into the already limited floor space.
However, this model continues to be one of the best selling eightleggers with about 20 per cent of the UK market. But by now Leyland must be considering a replacement of its dated cab. Perhaps when the T45 is launched the new model's cab shell will be used in the Routeman. This would not only provide a better standard of trim, but, more important, give better access than is presently provided by a very high step and narrow door opening. .
Steering effort, aided by a large diameter wheel and hydraulic power, was light while. the gear stick, park brake lever and good sized pedals are well placed, but I must criticise the positioning of the tipping controls to the right-hand rear of the driving position. The gap between the seat and side panel restricts access. It is difficult for those, like myself, unfamiliar with the controls, to see which switch operates the pto or the hydraulic ram.
Comfort tends to be a subjective assessment, but I liked the ride in the conditions encountered. The vehicle was especially comfortable when laden, and at higher speeds on good roads, body roll was minimal. Within the cab, engine and transmission noise sounded acceptably low.
Both the Reiver and Clydesdale share the Leyland G-cab. with similarly fitted body trims, cloth covered seats, rubber matting across the full width of the floor, and diagrammatic warning lights above the speedo and rev counter in the instrument panel.
An engine stop in the Reiver is located below the facia and much too close to the tipping control, on the right of the steering column. The gear stick, with puny splitter switch in the head, is long and often comes into contact with the driver's arm when he is using the intermediate gears.
Nearest in concept
On site this was the nearest in concept of the three test vehicles to the LD 55 in regular use. Plated at 24 tons gross, this 6X4 fitted with a high-capacity Tasktip alloy body was regularly laden with a payload of over 16,500kg (16.2 tons). A tipping cycle of just over 1 minute 10 seconds was recorded to discharge the load.
For mud plugging, a single steered axle presented less rolling resistance than the twin axles of the Routeman; the vehicle has a rear bogie of the same 18-ton capacity and lockable third differential.
Mirrors on the G-cabbed vehicles were badly sited and only the rear wheels could be seen. When reversing beneath a bucket loader it is important that the driver can see the arm of the loader in order to place the vehicle correctly.
First gear was needed when the vehicle was climbing the coalface, and as a precautionary measure we engaged the cliff-. lock. With a higher load height, body roll was no more noticeable than with the eightwheeler.
Gear changing is simple with a positive movement. The split-. continued overledf
ter allowed near maximum torque to be maintained up through the range to fifth gear, with overdrive sixth selected manually as with the full gears.
Although the engine provides only just over 4,4kW/ 'tonne (6bhp per ton) it was well up to the job in hand.
Full brake pressure was never used, but such braking that was necessary showed the system to be progressive and not too heavy.
All three vehicles were equipped with large treadle-type brake and throttle pedals, large enough to give a secure grip.
The much smaller Clydesdale was powered by the same 410 six-cylinder turbocharged diesel engine. With a Mackworth alloy tipping body piled high with the load we were some 3 7 20kg (3.66 tons) short of the maximum of 16,260kg (16 tons), with a payload of 7180kg (7.06 tons) so power was no problem.
The single drive axle might have got us into difficulty, but the graders kept the road clear so that by using first gear, over the early steep stage, we climbed out of the deep hole in fine style.
Journey time to the crusher took about 20 minutes as it had done with the two larger vehicles.
But tipping with the smal body and shorter run was, expected, quicker, taking obi 1 minute, which is all a academic on this type of ope tion where there is waiting tii involved at the loading and c charge points.
On the return, minus 1 load, the ride was much boi cier: the short wheelbase caw pitching.
However, the driving pc tion is good. The controls ; close to hand with the except of the tipping control. This placed much too far to the I beneath the facia. The driver to stretch fully in order to use As the bodybuilder fits tipping mechanism and t bodies it should only have tak a little more thought on his p to ensure that the switch coot is equally well mounted.
Daily inspections can made without lifting the cab just as well, although the c tilts it is securely bolted in 1 down position. A coolant header tank is ocated at the rear of the cab vhile the oil filler and dip stick ire reached beneath a hatch in he engine cowl. A separate ,ection within the glove-box louses the clutch reservoir. Exra storage space is provided by )oekets attached to the rear )anel.
Two local operators came king to give the vehicles the )nce-over. William Cowan, of Slamannan, a Leyland operator, bias first to arrive. He has about 30 vehicles operating on jeneral haulage and bulk trans)ort as well as his tipping inter?sts.
He has AECs, Guys, Reivers 3nd Clydesdales, some up to tight years' old, in his fleet. 3efore riding in the three iehicles we were driving, he Jaye me his clear impressions of he vehicles he operates.
The Clydesdale? It's a good otbing machine, he told me, 3nd spares are easy to get. But Dverheating with the Reivers.
410 engine had caused trouble in the past, and for this reason alone he was not keen on them. Bushes and shackles in the rear suspension need to be replaced every year, he said. If they are left too long damage can be caused to the chassis.
The Routeman? Access to the cab is bad, he said. Two of his drivers are around the 20-stone. continued overleaf
mark and in no way could he see them getting up that height with only one step placed above the wheel arch.
Modern cabs tilt, so a boltdown one is behind the times, he reckons. Although it normally takes only a few minutes to release the bolts, when they become seized it is a much longer job. In some instances, it has been necessary to cut the bolts off.
After riding in our vehicles he still liked the Clydesdale, was a little happier about the Reiver's. 410 engines after the reassurances from the Leyland representative on improvements, made to the engine, but still', maintained that availability of, spares needs improving.
I would say that the Routeman is value for money even with its dated cab and as he left I got the distinct impression that he is thinking of buying one.
The following day W. J. Collier, a haulage contractor arrived at the site. He too had experienced troubles with the 410 engine but, having made all the modifications as they had be'come available, has now overcome them. With his own five Reivers he has changed to 12.leaf suspension. With regular greasing of the suspension bushes, he claimed to get up to two years use from them.
He told me he has turned to other manufacturers over recent years, but after spending an hour in the Reiver he arranged. to have a demonstration, including motorway running, the following week.
Leyland has been only too aware of the problems of the 401/410 engines and has made a number of modifications to make the units reliable.
The most notable changes, that have already been introduced include a new cylinderhead gasket, a modified' cylinder-head casting and a large wax thermostat with a revised head clamping procedure.
I understand that Leyland is putting the final touches to its design improvement programme which will be recognised in the redesignation of the' engine titles later this year.
Little has been done to extend the life of the rear suspension, however, and regular greasing is still the only answer here.