Scots builders can still impress
Page 116
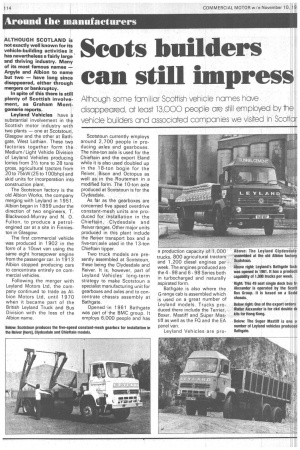
Page 117
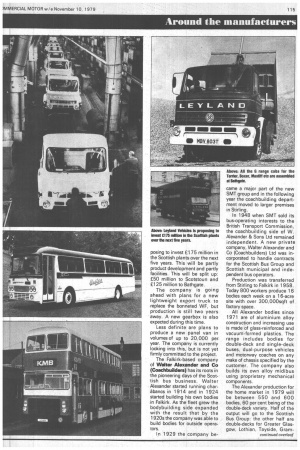
Page 118
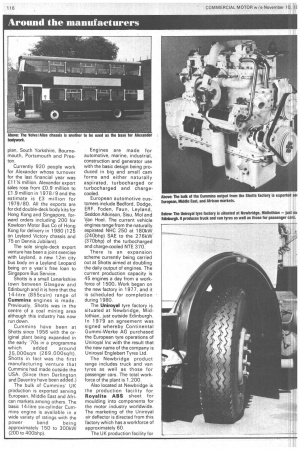
Page 119
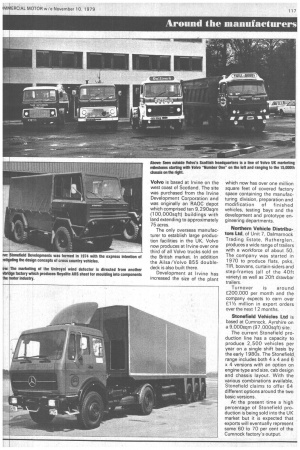
If you've noticed an error in this article please click here to report it so we can fix it.
Although some familiar Scothsh vehicle names have cisappeared, at least 13,000 people are still employec by ne vehicle builcers anc associatec companies we visited in Scotia
ALTHOUGH SCOTLAND is not exactly well known for its vehicle-building activities it has nevertheless a fairly large and thriving industry. Many of its most famous names -Argyle and Albion to name but two — have long since disappeared, either through mergers or bankruptcy.
in spite of this there is still plenty of Scottish involvement, as Graham Montgomerie reports.
Leyland Vehicles have a substantial involvement in the Scottish motor industry with two plants — one at Scotstoun, Glasgow and the other at Bathgate, West Lothian. These two factories together form the Medium/Light Vehicle Division of Leyland Vehicles producin lorries from 31/2 tons to 28 ton gross, agricultural tractors froth 20 to 75kW (25 to 100bhp) and skid units for incorporation into construction plant.
The Scotstoun factory is the old Albion Works, the company merging with Leyland in 1951. Albion began in 1899 under the direction of two engineers, T. Blackwood-Murray and N. 0. Fulton, to produce a petrolengined car at a site in Finnieston in Glasgow.
The first commercial vehicle was produced in 1 902 in the form of a 10cwt van using the same eight horsepower engine from the passenger car. In 1913 Albion stopped producing cars to concentrate entirely on commercial vehicles.
Following the merger with Leyland Motors Ltd, the com pany continued to trade as Al bion Motors Ltd, until 1970 when it became part of the British Leyland Truck and Bus Division with the loss of the Albion name. Scotstoun currently employs around 2,700 people in producing axles and gearboxes. The nine-ton axle is used for the Chieftain and the export Eland while it is also used doubled up in the 18-ton bogie for the Reiver, Bison and Octopus as well as in the Routeman in a modified form. The 10-ton axle produced at Scotstoun is for the Clydesdale.
As far as the gearboxes are concerned five speed overdrive constant-mesh units are produced for installation in the Chieftain, Clydesdale and Reiver ranges. Other major units produced in this plant include the Reiver transport box and a five-ton axle used in the 13-ton Chieftain tipper.
Two truck models are presently assembled at Scotstoun, these being the Clydesdale and Reiver. It is, however, part of Leyland Vehicles long-term strategy to make Scotstoun a specialist manufacturing unit for gearboxes and axles and to concentrate chassis assembly at Bathgate.
Opened in 1 961 Bathgate was part of the BMC group. It employs 6,000 people and has a production capacity of 1,000 trucks, 800 agricultural tractors and 1,200 diesel engines per week. The engines produced are the 4-98 and 6 98 Series both in turbocharged and naturally aspirated form.
Bathgate is also where the Grange cab is assembled which is used on a great number of Leyland models. Trucks produced there include the Terrier, Boxer, Mastiff and Super Mastiff as well as the FQ and the EA panel van.
Leyland Vehicles are pro
posing to invest £175 million in the Scottish plants over the next five years. This will be partly product development and partly facilities. This will be split up: £50 million to Scotstoun and £125 million to Bathgate.
The company is going ahead with plans for a new lightweight export truck to replace the bonneted WE, but production is still two years away. A new gearbox is also expected during this time.
Less definite are plans to produce a new panel van in volumes of up to 20,000 per year. The company is currently looking into this, but is not yet firmly committed to the project.
The Falkirk-based company of Walter Alexander and Co (Coachbuilders) has its roots in the pioneering days of the Scottish bus business. Walter Alexander started running charabancs in 1914 and in 1924 started building his own bodies in Falkirk. As the fleet grew the bodybuilding side expanded with the result that by the 1920s the company was able to build bodies for outside operators.
In 1929 the company be
came a major part of the new SMT group and in the following year the coachbuilding department moved to larger premises in Stirling.
In 1948 when SMT sold its bus-operating interests to the British Transport Commission, the coachbuilding side of W. Alexander & Sons Ltd remained independent. A new private company, Walter Alexander and Co (Coachbuilders) Ltd was incorporated to handle contracts for the Scottish Bus Group and Scottish municipal and independent bus operators.
Production was transferred from Stirling to Falkirk in 1958. Today 800 workers produce 16 bodies each week on a 16-acre site with over 300,000sgft of factory space.
All Alexander bodies since 1971 are of aluminium alloy construction and increasing use is made of glass-reinforced and vacuum-formed plastics. The range includes bodies for double-deck and single-deck buses, dual-purpose vehicles and motorway coaches on any make of chassis specified by the customer. The company also builds its own alloy midibus using proprietary mechanical components.
The Alexander production for the home market in 1979 will be between 550 and 600 bodies, 60 per cent being of the double-deck variety. Half of the output will go to the Scottish Bus Group: the other half are double-decks for Greater Glasgow, Lothian, Tayside, Gram pian, South Yorkshire, Bournemouth, Portsmouth and Preston.
Currently 920 people work for Alexander whose turnover for the last financial year was £111/4 million. Alexander export sales rose from £0.9 million to £1.9 million in 1978/9 and the estimate is £3 million for 1979/80. All the exports are for ckd double-deck body kits for Hong Kong and Singapore, forward orders including 200 for Kowloon Motor Bus Co of Hong Kong for delivery in 1980 (125 on Leyland Victory chassis and 75 on Dennis Jubilant).
The sole single-deck export venture has been a joint exercise with Leyland, a new 12m city bus body on a Leyland Leopard being on a year's free loan to Singapore Bus Service_
Shotts is a small Lanarkshire town between Glasgow and Edinburgh and it is here that the 14-litre (855cuin) range of Cummins engines is made. Previously, Shotts was in the centre of a coal mining area although this industry has now run down.
Cummins have been at Shotts since 1956 with the original plant being expanded in the early '70s in a programme which added around 25,000sqm (269,000sqft). Shotts in fact was the first manufacturing venture that Cummins had made outside the USA. (Since then Darlington_ and Daventry have been added.) The bulk of Cummins' UK production is exported serving European, Middle East and Afri can markets among others. The basic 14-litre six-cylinder Cum mins engine is available in a wide variety of ratings with the power band being approximately 150 to 300kW (200 to 400bhp). Engines are made for automotive, marine, industrial, construction and generator use with the basic design being produced in big and small cam forms and either naturally aspirated, turbocharged or turbocharged and chargecooled.
European automotive customers include Bedford, Dodge, ERF, Foden, Faun, Leyland, Seddon Atkinson, Sisu, Mol and Van Hool. The current vehicle engines range from the naturally. aspirated NHC 250 at 180kW, (240bhp) SAE to the 276kW (370bhp) of the turbocharged and charge-cooled NTE 370.
There is an expansion scheme currently being carried out at Shotts aimed at doubling the daily output of engines. The current production capacity is 45 engines a day from a workforce of 1500. Work began on the new factory in 1977, and it is scheduled for completion • during 1980.
The Uniroyal tyre factory is situated at Newbridge, Midlothian, just outside Edinburgh. In 1979 an agreement was signed whereby Continental Gummi-Werke AG purchased the European tyre operations of Uniroyal Inc with the result that the new name of the company is Uniroyal Englebert Tyres Ltd.
The Newbridge product range includes truck and van tyres as well as those for passenger cars. The total workforce of the plant is 1,200.
Also located at Newbridge is the production facility for Royalite ABS sheet for moulding into components for the motor industry worldwide. The marketing of the Uniroyal air deflector is directed from this factory which has a workforce of approximately 60.
The UK production facility for Volvo is based at Irvine on the west coast of Scotland. The site was purchased from the Irvine Development Corporation and was originally an RAOC depot which comprised ten 9,290sqm (100,000sqft) buildings with land extending to approximately 75 acres.
The only overseas manufacturer to establish large production facilities in the UK, Volvo now produces at Irvine over one third of all Volvo trucks sold on the British market. In addition the Ailsa /Volvo B55 doubledeck is also built there.
Development at Irvine has increased the size of the plant which now has over one million square feet of covered factory space containing the manufacturing division, preparation and modification of finished vehicles, testing bays and the development and prototype engineering departments.
Northern Vehicle Distributors Ltd, of Unit 7, Dalmarnock Trading Estate, Rutherglen, produces a wide range of trailers with a workforce of about 50. The company was started in 1 970 to produce flats, psks, TIR, boxvans, curtain-siders and step-frames (all of the 40ft variety) as well as 20ft drawbar trailers.
Turnover is around £200,000 per month and the company expects to earn over £11/2 million in export orders over the next 12 months.
Stonefield Vehicles Ltd is based at Cumnock, Ayrshire on a 9,000sqm (97,000sqft) site.
The current Stonefield production line has a capacity to produce 2,500 vehicles per year on a single shift basis by the early 1980s. The Stonefield, range includes both 4 x 4 and 6 x 4 versions with an option on engine type and size, cab design and chassis layout. With the various combinations available, Stonefield claims to offer 64 different options around the two basic versions.
At the present time a high percentage of Stonefield production is being sold into the UK market but it is expected that exports will eventually represent some 60 to 70 per cent of the Cumnock factory's output.