The Case-Hardening, Annealing and Tem pering of Steel.
Page 5
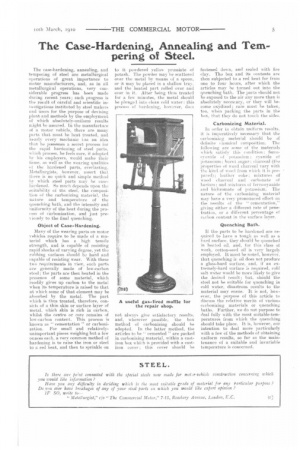
Page 6
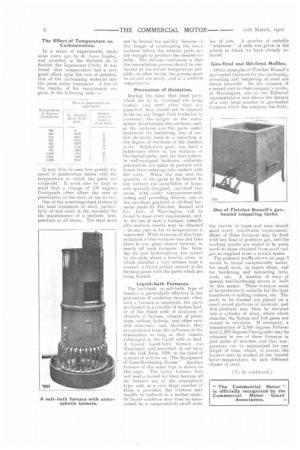
If you've noticed an error in this article please click here to report it so we can fix it.
The case-hardening, annealing, and tempering of steel are metallurgical .operations of great importanceto motor manufacturers, and, as in all metallurgical operations, very considerable progress has been made during recent years; such progress is the result of careful and scientific investigations instituted by steel makers and users for the purpose of devising plant and methods by the employment of which absolutely-uniferm results might be assured. in the manufacture of a motor vehicle, there are many pots that must be heat trented, and
-nearly every mechanic an idea that be poesessee a secret process for the rapid hardening of steel parts, which process, he feels sure, it adopted by his employers, would make their fame. as well as the wearing qualities ci the hardened parts, everlasting. Metallurgists, however, assert that there ie no quick and simple method by which steel parts may he casehardened. So much depends upon the suitability of the, steel, the composition of the carbonizing material, the nature and temperature of the quenching bath, and the intensity and -uniformity of the beat during the process of carbonization, and just previously to the final quenching.
Object of Case-Hardening.
Many of the wearing parts on motor vehicles require to be made of a material which has a high tensile strength, and is eapable of resisting rapid shocks of varying degree, yet the rubbing surfaces should bc hard and capable of resisting wear. With these two requirements in view, such parts are generally made of low-carbon steel ; the parts are then heated in the presence of some material, which readily gives up carbon to the metal when its temperature is raised to that at which some of that element may be absorbed by the metal. The part which is thus treated, therefore, consists of a thin skin or surface layer of metal, which skin is rich in carbon, whilst the centre or core remains of low-carbon content. This process is known as " cementation " or carbonization. For small and relativelyunimportant pieces weighing but a few ounces each, is very common method of hardening is to raise the iron or steel to a red heat, and then to sprinkle on to it powdered yellow prus.siate of potash. The powder may be scattered over the metal by means of a spoon, or it may be placed in a shallow tray. and the heated part rolled over and over in it. After being thus treated for a few minutes, the metal should be plunged into clean cold water : this process of hardening, however, does
not always give satisfactory results, and, wherever possible, the box method of carbonizing should he adopted. In the latter method, the articles to 1ie'• cemented " are packed in carbonizing material, within a eastiron box which is provided with a castiton cover ; tins enyer should he
fastened doe n, and scaled with fire clay. The box and its contents are then subjected to a red heat for front one to four hours, after which the articles may he turned out into the quenching bath, The parts should not be exposed to the air any snore than is absolutely necessary, or they will become oxydized; care must Le taken, too, when packing the parts in the box, that they do not touch the sides.
Carbonizing Material.
In order to obtain uniform results, it is imperatively necessary that the carbonizing material should be of definite 1 teenticni compoeition. The following are sonic of the materials whieh satisfy this cendition ferrocyenide if pot assi tun ; cyanide of pet a ssi um ; burnt sugar ; charcoal (the properties of wood charcoal vary with the Ic hid sf wood from witiett it is prepared); leather coke ; mixtures: of e-oral charcoal and carbonate of barium ; and mixtures of ferru-cyanide and hichromate of potassium. The nature of the carbonizing material may have a very pronounced effect on the results of the " cementation," giving, either a different rate of penetration, or a different percentage of carbon content in the surface layer.
Quenching Bath.
If the parts to he hardened are required to have a tough as well as a hard surface. they should be quenched in heated oil, and, for this class of work, cotton-seed oil is very largely employed. It must be noted, however, that quenching iu oil does not produce a glass-hard surface, and, if an extremely-hard surface is required, cold salt water would be more likely to give the desired result; but, should the steel not be suitable for quenching in cold water, disastrous results to the material may ensue: It is not, however, the purpose of this article to discuss the relative merits of varioue carbonizing materials or quenching baths. Further, we do not purpose to deal fully with the most suitable-temperatures from which the quenching should take place. It is, however, our intention to deal more particularly with a few of the methods of obtaining uniform results, so far as the maintenance of a suitable and invariable temperature is concerned.
The Effect of Temperature on Carbonization.
In a series of experiments, made sonic years ago by at . Leon Guillet, and recorded in the Bulletin de la Societe des Ingenieurs Civils, it was found that temperature had a very great effect upon the rate of penetration of the carbonizing material into the parts under treatment A few of the results of his experiments are given in the following table:—
It may thus be seen how greatly the speed of penetration varies with the temperature to which the parts are subjected. It must also be kept in mind that a change of 100 degrees Centigrade often alters the rate of penetratioe in the ratio of one to two.
One of the most-important factors in the heat treatment of steel, particleittrIy of tool steel, is the necessity for the maintenance of a uniform temperature at all times. The steel must
not be heated too quickly, because et the danger of overheating the outer surfaces before the interior parts are hot enough to produce the desired results. The olivions conelusion is that the cementation process should be conducted at the lowest temperature possible ; in other wcrds, the process must be carried out slue ly, and at a uniform temperati!re.
Prevention of Oxidation.
During the time that steel part.' which are to be hardened are being heated, and until after they are quenched, they should not be exposed to the air any longer than is absolutely necessary; the oxygen in the atmosphere decarbonizes the surfaces, and, as the surfaces are the parts under treatment for hardening, loss of carbon obviously leads to a reduction in the degree of hardness of the finished parts, Sulphurous gases, too, have a deleterious effect on the surfaces of the heated parts, and, for that reason, in well-equipped factories, elaborate precautions are taken to prevent such fumes from entering into contact with the work. When the size and the quantity el the parts to be heated do not werrant time installation of large, and specially-designed, coal-fired furnaces, with eostly temperature-indicating arid recording devices, one of the excellent gas-fired or oil-fired furnaces made by Fletcher, Russell and Co.. Ltd., of Warrington, will be found to meet every requirement, and, by the use of such a furnace, remarkably-uniform results may be obtained —at any rate so for as temperature is concerned. With furnaces of this type, oxidation of the surfaces does not take place to any great extent because, in nearly all such furnaces the burning air tied hydrocarbons are caused to circulate about a fireclay oven, in which chamber a very intense heat is treated. withnut actual contact of the burning gases with the parts which are being heated,
Liquid-bath Furnaces.
The lead-bath, or salt-both, type of furnace is particularly effective in the prevention of oxidation because, when such a furnace is employed, the parts are heated in a crucible of molten lead. or of the fused salts of mixtures of chloride of barium, chloride of potassium, sodium hydrate, and other suitable materials, and, therefore, they are protected from the influence of the atmosphere so long as they remain submerged in the liquid salts or lead. A typieal liquid-bath furnace was illustrated, and described, in our issue of the 11th June, 1008, in the third of a series of articles on "The Equipment of Case-Hardening Rooms.' Another furnacee, of the same type is shown an this page. The latter furnace does not need a furred air blast because all its burner's are of the atmospheric type, and, as a very large number of them is provided, the mixture may rapidly be reduced to a molten state; its liquid condition may then he maintained by a comparatively-small num
her of jets. A number of suitable " mixtures " of salts was given in the article to which we have already referred.
Gas-fired and Oil-fired Muffles.
Other examples of Fletcher Russell's gas-heated furnaces for the hardening, annealing and tempering of steel are shown herewith. On the occasion of a recent visit to that company's works, at -Warrington, one of our Editorial representatives was shown the designs of a very large number of gas-heated furnaces which the company has built; the variety of types and sizes should meet every conceivable requirement. Many of these furnaces may be fired with any kind of producer gas, and the working results are stated to be quite equal to those obtained from good coal gas as supplied from a town's mains. The pedestal muffle shown on page 5 would be found exceptionally useful, for small work, in repair shops, and for hardening and tempering lathe tools, etc. A number of sizes of special tool-hardening stoves is built by this maker. These furnaces seem to be particularly suitable for the heat treatment -of milling cutters, etc. The parts to be treated are placed on a small round platform of firebrick, and this platform may then be elevated into a cylinder of silica, about which chamber the flames and hot gases are caused to circulate. If necessary, a temperature of 2,500 degrees Fahrenheit (1,370 degrees Centigrade) may be obtained in one of these furnaces in just under 45 minutes, and that temperature can be maintained for any length of time, whilst, of course, the furnace may be worked at any desired lower temperature, to suit different classes of steel.