The turbine challenge
Page 43
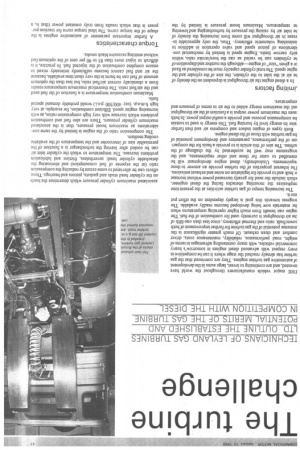
Page 44
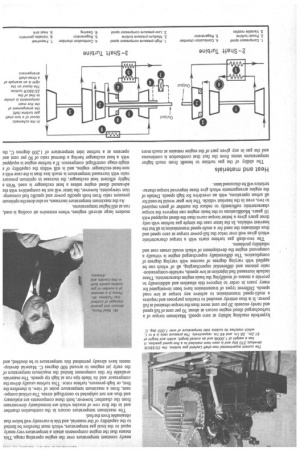
Page 45
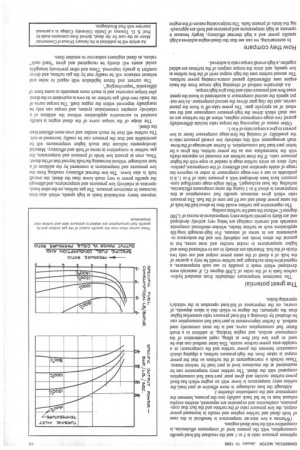
If you've noticed an error in this article please click here to report it so we can fix it.
TECHNICIANS OF LEYLAND GAS TURBINES LTD. OUTLINE THE ESTABLISHED AND POTENTIAL MERITS OF THE GAS TURBINE IN COMPETITION WITH THE DIESEL
WE major vehicle manufacturers throughout the world have mvested, and are continuing to invest, large sums in the development pf automotive gas turbine engines. They are convinced that the gas turbine has already reached the stage where it can be competitive in every respect with advanced diesel engines in tomorrow's heavy commercial vehicles, with many outstanding advantages in terms of weight, road performance, reliability, maintenance costs, driver :ornfort and clean exhaust. Of much greater significance is the mmense potential of the gas turbine for further improvement of both )ower/bulk ratio and thermal efficiency, since less than one-fifth of be air throughput is currently used for combustion of the fuel. The engine can benefit from much higher operating temperatures when Ire materials now being developed become readily available. The )rogress towards this goal is largely dependent on the effort put nto it.
The increasing tempo of gas turbine activities at the present time fliiphasizes the mounting obstacles facing the diesel engineer, which include the need for greatly increased power without increase n bulk and to provide for legislation on noise and exhaust emissions. l'he inherent properties of the turbine provide an answer to these .equirements. Undoubtedly, diesel engine development will be ntensified to cater for these and other requirements, and the )rogramme may well be accelerated by the challenge of the urbine. The aim of this article is to provide a basis for the compari;on of the performance, parameters and development potential of he gas turbine with those of the diesel engine.
Both types of engine induce and compress air and then further .aise its energy level by burning fuel. This energy is used to sustain he compression process and provide a useful output power. In both :ases the maximum power output is a function of the air throughput Ind the maximum energy added to the air in terms of pressure and emperature.
m iting factors
In a diesel engine the air throughput is dependent on the density of he air at the inlet to the cylinder, the size of the cylinder and the ngine speed. The total cylinder capacity must be considered as rued Dr a given "size" of engine—although the number and disposition of he cylinders can be varied as can the bore/stroke ratio, within airly narrow limits. Engine speed is limited by mechanical coniderations of piston speed and valve operation in addition to iminishing volumetric efficiency. Thus, the only appreciable inrease in air throughput will come from increasing the density of he inlet air by raising the pressure by turbocharging and lowering 'le temperature. Maximum boost pressure is limited by the associated maximum cylinder pressure which determines the loads on the cylinder head studs and gaskets, pistons and bearings. These effects can be alleviated to some extent by reducing the compression ratio (at the expense of fuel consumption) and eliminating the detachable cylinder head; nevertheless, friction and lubrication problems increase. The temperature to which the cylinder inlet air can be cooled after leaving the turbocharger is a function of the permissible size of intercooler and the temperature of the available cooling medium.
The compression ratio of the engine is limited by the same considerations as maximum boost pressure, that is the associated maximum cylinder pressure. There are also fuel and combustion problems which increase with very high compression ratios, as with increasing engine speed. Efficient combustion, for example, at very high b.m.e.p. (say 400/500 p.s.i.) would probably demand special fuels.
Maximum combustion temperature is a function of the fuel used and the air/fuel ratio. The theoretical maximum temperature results from a chemically correct air/fuel ratio, but less than the optimum amount of fuel can be burnt in the very short time available, because the air and fuel cannot become sufficiently intimately mixed to ensure complete combustion of the injected fuel. In practice, it is difficult to inject more than 85 to 90 per cent of the optimum fuel without emitting excessive black smoke.
Torque characteristics
A further important parameter of automotive engines is the shape of the torque curve. The ideal torque curve for traction pur poses is that which results from truly constant power (that is, a hyperbola reaching infinity at zero speed). Maximum torque of a turbocharged diesel engine occurs at about 70 per cent of full speed and rarely exceeds 20 per cent more than the torque obtained at full power. It is thus entirely unsuited to traction purposes and requires a multi-speed transmission to achieve any torque at low road speeds. Different types of transmission have been investigated for many years in order to improve this situation and additionally to provide a means of modifying the basic engine characteristic. These include increased fuel injection at low speeds, variable-compressionratio pistons and differential supercharging, all of which can be applied with varying degrees of success with varying degrees of complication. The differentially supercharged engine is virtually a compound engine the development of which would create cost and reliability problems.
The two-shaft gas turbine starts with a torque characteristic which gives well over twice the full-power torque at zero speed and thus eliminates the need for a multi-speed transmission in all but the heaviest vehicles. In the latter case the simple gas turbine with only three gears gives a better torque curve than the diesel equipped with 10 gears. Modifications to the basic engine can improve the torque characteristic sufficiently to reduce the number of gears required to two, even in the heaviest vehicle. The low gear would be used for all urban operations, with an overdrive for high speeds. Details of the engine arrangements which give these improved torque characteristics will be discussed later.
Heat and materials
The ability of the gas turbine to benefit from much higher temperatures stems from the fact that combustion is continuous and the gas in any given part of the engine remains at much more nearly constant temperature over the engine operating range. This means that the engine components attain a temperature very nearly equal to the local gas temperature, which must therefore be limited to the capability of the material, and this is currently well below that obtainable from the fuel.
The maximum temperature occurs in the combustion chamber and in the first row of nozzles which are immediately downstream from the chamber; however, both these components are stationary and thus are not subjected to centrifugal stress. The critical component, from a maximum temperature point of view, is therefore the first, or high-pressure, turbine rotor. This turbine usually drives the compressor and its blade tips run at high tip speeds. The materials available for this component limited the maximum temperature of the early jet engines to around 600 degrees C. Material developments have already permitted this temperature to be doubled, and modern large aircraft engines, where extensive air cooling is used, run at still higher temperatures.
As the maximum temperature increases, so also does the optimum pressure ratio from both specific power and specific fuel consumption viewpoints; however, the latter will not be competitive with the advanced diesel engine unless a heat exchanger is used. With a highly efficient heat exchanger, the increase in optimum pressure ratio with increased temperature is much less than is the case with a non-heat-exchanger engine, and is still within the capability of a single-stage centrifugal compressor. If a turbine engine is equipped with a heat exchanger having a thermal ratio of 90 per cent and operates at a turbine inlet temperature of 1,200 degrees C, tit( optimum pressure ratio is 5 to 1 and the resultant full-load specific consumption, with the present level of component efficiencies, is competitive with the best diesel engines.
(Whereas a low inlet-air temperature is beneficial in the case of both diesel and turbine engines and results in increased power output, the low pressure ratio of the turbine and the fact that compression, combustion and expansion are separated, enables surplus exhaust heat to be fed back usefully into the process, between the compressor and the combustion chamber.) Although the heat exchanger is more effective at part load, the turbine entry temperature is lower with an engine which has fixed power-turbine nozzles and gives poor part-load fuel consumption compared with the diesel. The turbine entry temperature can be maintained at the maximum level at part load by various means. These include a rearrangement of the turbines so that the power output is taken from the high-pressure turbine; a slipping clutch connection between the power turbine and the compressor; or a variable-area power-turbine nozzle. This latter method can also be used to give low fuel flow at idling, rapid acceleration of the compressor section, and engine braking, in addition to a much flatter fuel consumption curve, and is the most commonly used method. A further improvement in part-load fuel consumption can be obtained by choosing a full-load pressure ratio somewhat higher than the optimum; the degree to which this is taken depends, of course, on the importance of full-load operation in the vehicle's operating duties.
The great potential
The maximum temperature obtainable from standard hydrocarbon fuels is of the order of 2,500 degrees C; if materials were developed which made it possible to use such temperatures, a regenerative-heat-exchanger gas turbine would be only a quarter of the bulk of a diesel of the same power output and use only two thirds of the fuel. Materials are already in use to withstand these and higher temperatures in rocket nozzles and nose cones, but in general the stress levels are relatively low and the endurance requirements are in terms of minutes. For high-strength long-life applications such as turbine blades, whisker-reinforced composite materials and ceramic coatings are being very actively developed and are likely to permit turbine entry temperatures in excess of 1,500 degrees C without the need for turbine cooling.
The regenerative gas turbine would then be about half the bulk of the same power diesel and use 85 per cent of the fuel. The pressure ratio which gives minimum specific fuel consumption at this temperature is about 8 to 1 (using the same component efficiencies, including the heat exchanger). While single-stage centrifugal compressors have been developed with a pressure ratio of 8 to 1, it is preferable to use a two-stage compressor in order to improve the range of stable operation and efficiency of the compressor, particularly since an extra turbine stage is needed to cope with the higher pressure ratio. If the three turbines are mounted on separate shafts with the intermediate one as the power turbine, this gives a far better part-load fuel consumption. A further advantage of the threeshaft arrangement with this relatively low overall pressure ratio is the possibility of running the first-stage compressor faster at low powers to give a torque ratio of 4 to 1.
Other means of improving the torque ratio include differentially geared two-stage-compressor engines, where all the turbines are on one shaft which drives the high-pressure compressor and the sun wheel of an epicyclic gear. The power-take-off is from the planet carrier, and the ring gear drives the second compressor. At low output speeds the second compressor is accelerated to boost the speedmass flow and pressure ratio and thus give high torque.
An alternative method of obtaining high torque from the basic engine uses differentially geared contra-rotating power turbines. The second turbine uses the high output swirl of the first turbine at low speeds, and since the torque outputs of the turbines are added together, a high overall torque ratio is achieved.
How they compare
In summarizing, we can see that the diesel engine achieves a high specific power and a high thermal efficiency, largely because it operates at high temperatures and pressures and both are approaching the limits of present fuels. The reciprocating nature of the engine
imposes heavy mechanical loads at high speeds, which also limit increases in maximum pressure. The gas turbine, on the other hand, operates at relatively low pressures and temperatures, and although the specific power is very much lower than the diesel, the overall bulk is also lower. The low thermal efficiency resulting from the low pressures and temperatures is countered by the addition of a heat exchanger without increasing the bulk beyond that of the diesel. Thus, even at present low levels of pressure and temperature, the gas turbine is competitive in terms of bulk and'efficiency. Material developments indicate that much higher temperatures will be permissible and that the pressure can be readily increased to suit. The turbine will then be much smaller and even more efficient than the diesel.
The shape of the torque curve of the diesel engine is totally unsuited to automotive applications without the addition of a relatively complex transmission system, and torque can only be marginally improved within the engine itself. The torque curve of the basic two-shaft gas turbine on its own is equivalent to the diesel plus torque converter and is much more amenable to some form of differential "supercharging".
The current and future legislation with regard to noise and exhaust emission will be readily met by the gas turbine, and driver comfort is greatly improved. These and other previously intangible social assets will shortly be recognized and given "hard cash" values, as diesel engineers endeavour to emulate them.