Road and workshop
Page 41
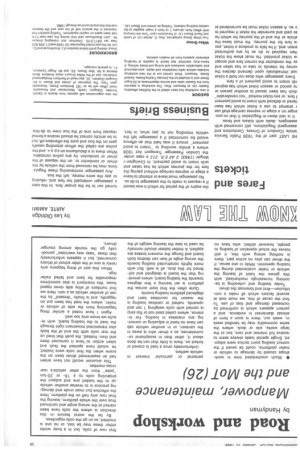
If you've noticed an error in this article please click here to report it so we can fix it.
by Handyman
Manpower, maintenance
and the MoT (26)
• Much unscheduled time in workshops caused by damage to vehicle or trailer platforms, could be saved if the correct loading point tactics were adopted. Single special loads always seem to receive full interest and care, but at the large works, site or dock, where the same commodity may be handled week in, week out, there is soon a form of almost disinterest in evidence, and a pattern appears which is confirmed by increased damage and loss of use. To find the cause of this, we must look at several factors which all make a contribution—first and foremost the driver.
Today loading and unloading is becoming increasingly mechanized, with this grows the habit of leaving the vehicle or trailer unattended during the loading operation. While in one sense, if the driver can play no active part, there is nothing wrong with this, it still leaves the actual operation of loading to people, however skilled, who have no personal or particular interest in vehicle welfare.
Unfortunately once a load is craned or forked on, there is little that can be done about it, other than in exceptional circumstances, so a driver who is away in the canteen, or in another vehicle cab can have no hand in adjusting or correcting any mistakes in loading. For instance, where coiled steel rod or flat strip is carried with coils weighing 1 ton and upwards, rushed or careless loading is the reason for countless bent and displaced platform loading boards.
Quite often the first layer across the platform is set leaning a few degrees towards the loading board, where providing that the board is designed and stiffened for this duty, all is well. But with more lightly constructed loading boards the wrong angle of lean can destroy both board and fixings the moment brakes are applied. A timber bolster should normally be used to take the leaning weight of the first row of coils, but in a busy works either these may be lost, or no one is troubled, so on go the coils regardless.
By far the worst feature in this direction is where the coils have been started at the wrong angle and continued thus over the whole platform, leaving the final row only half on the platform. Here the effective but most crude and damaging practice is to reverse another vehicle up to the loaded one and subject the projecting coils to a 15or 20-ton "'poke" from the other vehicle's rear cross-member.
This situation would not have arisen had an experienced driver been on the scene when the first coils were loaded; he would have spotted the fault and taken action to have it corrected there and then. Instead, the push that lined up the rear coils with the end of the body also transmitted movement right through the load to the loading board, with results we know only too well.
Again I have noted a similar thing happening from the side of vehicle or trailer, where the load has been put on raggedly, and is finally "dressed" by the use of another vehicle as a ram. Here we find numbers of alloy side raves ripped loose; this treatment is also sometimes responsible for bent and failed trailer legs.
When this sort of thing happens only rarely is one of the older school of drivers concerned, but it appears unfortunately that these "easy way exercises" periodically go the rounds among younger drivers.