Progress with plywood
Page 40
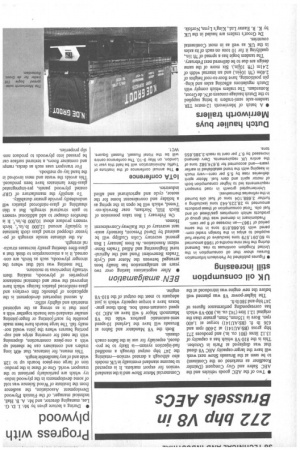
If you've noticed an error in this article please click here to report it so we can fix it.
• During a lecture given by Mr. I. D. G. Lee, managing director, and Mr. A. B. Hall, technical manager, of the Finnish Plywood Development Association, the audience from the Institute of Wood Science was told of some developments in the plywood industry which are particularly pertinent to the transport world. One of these is the production of large one-piece boards up to 12ft wide and of any handleable length.
This means, for instance, that 40ft long trailers and containers can be sheeted up with a one-piece construction, dispensing with the need for covering strips and supporting bearers where the joins would normally fall. The large boards have been made possible by scarf-jointing or finger-jointing smaller standard-size boards together with a joint that is as strong as the unjointed materials and slightly stiffer.
A second important development is the application of phenolic film overlays and glass-reinforced plastics facings which have improved the wear and chemical resistance properties of plywoods, making them virtually impervious to moisture.
The meeting was told that where the stronger plywoods, such as birch, are concerned, it is a misconception to think that a glass-fibre sheeting greatly increases structural strength.
As the ultimate tensile strength of polyester chopped strand glass cloth laminate is typically around 12,000 lb /in.', birch veneers produce about 10.000 lb /in.'. It is therefore cheaper to add additional veneers to gain structural strength. But a thin sheathing of glass-reinforced plastics will undoubtedly provide greater durability.
To simplify the manufacture of GRP coated plywood panels, pre-impregnated glass-fibre laminates have been produced. This avoids the waste and mess involved in the hand lay-up methods.
For transport uses such as decks, ramp. and container floors, a textured surface car be pressed into plywoods to produce nonslip properties.