Steel and Tool Advances Reviewed
Page 50
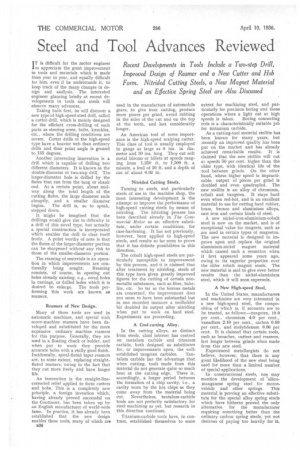
If you've noticed an error in this article please click here to report it so we can fix it.
Recent Developments in Tools Include a Two-step Drill, Improved Design of Reamer and a New Cutter and Hob Fain. Nitrided Cutting Steels, a New Magnet Material and an Effective Spring Steel are Also Discussed IT is difficult for the motor engineer I to appreciate the great improvement in tools and materials which is made from year to year, and equally difficult for him, even if he understands it, to keep track of the many changes in desin and analysis. The interested engineer glancing briefly at recent developments in tools and steels will observe many advances.
Taking tools first, he will discover a new type of high-speed-steel drill, called a, cotter drill, which is mainly designed for the efficient cross-drilling of such parts as steering arms, bolts, knuckles, etc., where the drilling conditions are severe. Cotter drills of the high-speed type have a heavier web than ordinary drills and their point angle is ground to 135 degrees.
Another interesting innovation is a drill which is capable of drilling two different diameters. It is known as the double-diameter or two-step drill. The larger-diameter hole is drilled by the flutes that run from the tang or shank end. At a certain point, about midway along the total length of the cutting flutes, the large diameter ends abruptly, and a smaller diameter begins. The drill is, so to speak, stepped down.
it might be imagined that the drillings would give rise to difficulty in a drill of this novel type, but actually a special construction is incorporated which enables the drill to clear itself freely. A point worthy of note is that the flutes of the larger-diameter portion can be sharpened without any risk to those of the smaller-diameter portion.
The reaming of materials is an operation in which improvements are continually being sought. Reaming consists, of course, in opening out holes already existing, e.g., cored holes in castings, or drilled holes which it is desired to enlarge. The tools performing this work are known as reamers.
Reamers of New Design.
Many of these tools are used in automatic machines, and special stub, screw-machine reamers have been developed and substituted for the more expensive ordinary machine reamers for this purpose. Generally, they are used in a floating chuck or holder, and when put to work they provide accurate holes with a really good finish. Incidentally, spiral-fluted taper reamers are, to some extent, replacing straight. fluted reamers, owing to the fact that they cut more freely and have longer life.
An innovation is the straight-linecorrected relief applied to form cutters and hobs. This is a completely new principle, a foreign invention which, having already 'proved successful on the Continent, has been taken up by an English manufacturer of world-wide fame. In practice, it has already been established that the new design enables these tools, many of which are a36 used in the manufacture of automobile gears, to give freer cutting, produce more pieces per grind, avoid rubbing in the sides of the cut and on the top of the teeth, and last considerably longer.
An American tool of some importance is the high-speed scalping cutter. This class of tool is usually employed in gangs as large as 8 ins, in diameter and 80 ins. long. They cut soft metal blooms or billets at speeds ranging from 1,250 ft. to 1,500 ft. a minute, a feed of 20 ft. and a depth of cut of about 0.02 in.
Nitrided Cutting Steels.
Turning to steels, and particularly steels of use in the machine shop, the most interesting development is the attempt to improve the performance of high-speed cutting steels by means of nitriding. The nitriding process has been described already in The Commercial Motor as an effective substitute, under certain conditions, for case-hardening. It has not previously, however, been applied to high-speed steels, and results so far seem to prove that it has definite possibilities in this direction.
The cobalt high-speed steels are particularly susceptible to improvement by this process, and it is claimed that after treatment by nitriding, steels of this type have given greatly improved figures for the cutting of certain nonmetallic substances, such as fibre, bakelite, etc. So far as the ferrous metals are concerned, the improvement does not seem to have been substantial but in one recorded instance a toolholder bit doubled its output after nitriding when put to work on hard steel. Experiments are proceeding.
A Cool-cutting Alloy.
In the cutting alloys, as distinct from steels, chief interest has centred on tantalum carbide and titanium carbide, both designed as substitutes for, or improvements upon, the well
established tungsten carbides. Tantalum carbide has the advantage that when cutting, tools made from this material do not generate quite so much heat at the cutting edge. There is, accordingly, a longer period between the formation of a chip cavity, i.e., a cavity worn by the hot chips as they come away from the material being cut. Nevertheless, tantalum-carbide tools are not perfectly satisfactory for steel machining as yet, but research in this direction continues.
Titanium-carbide tools have, in contrast, established themselves to some extent for machining steel, and particularly for precision boring and those operations where a light cut at high speeds is taken. Boring connecting rods is a characteristically suitable job for tintanium carbide.
As a cutting-tool material stelae has been known for many years, but recently an improved quality has been put on the market and has already achieved remarkable results. It is claimed that the new stellite will cut at speeds 50 per cent, higher than the older type, with identical life of the tool between grinds. On the other hand, where higher speed is impracticable, output of pieces per grind is doubled and even quadrupled. The new stellite is an alloy of chromium, cobalt and tungsten. It stays hard even when red-hot, and is an excellent material to use for cutting hard rubber, brass, bronze and aluminium alloys, cast iron and certain kinds of steel.
A new nickel-iron-aluminium-cobalt steel is now on the market, and is of exceptional value for magnets, such as are used in certain types of magnetos. The new material is designed to improve upon and replace the original aluminium-nickel magnet material which caused such a sensation when it first appeared some years ago, owing to its superior properties over the older cobalt magnet steels. The new material is said to give even better results than the nickel-aluminium steel, which it will soon supersede.
A New High-speed Steel.
In the United States, manufacturers and machinists are very interested in a new high-speed steel, the composition of which is, if accounts are to he trusted, as follows:—tungsten, 19.0 per cent., chromium 4;0 per cent., vanadium 2.10 per cent., carbon 0,80 per cent., and molybdenum 0,60 per cent. It is claimed that certain tools, such as broaches, cutters and reamers, last longer between grinds when made from this new steel.
Experienced metallurgists do not believe, .however, that there is any great likelihood of the new steel being used for more than a limited number, of special applications.
In constructional steels, one may mention the development of 'silicamanganese spring steel for motorvehicle and other springs. This material is proving an effective substitute for the special alloy spring steels which have hitherto proved the only alternative for the manufacturer requiring something better than the ordinary carbon spring steels, yet not desirous of paying too heavily for it,